はじめに
庫内作業の現場には、「人によってやり方が違う」「属人的なコツでなんとかしている」「口頭伝承が基本」という課題が根深く残っています。とくに、複数の派遣スタッフやパートタイム作業員が日々入れ替わる倉庫では、“共通ルールがない”こと自体が非効率の原因となり、在庫差異やミスの温床になります。
この記事では、社内SEとして現場改善に関わった私が「作業の標準化」をどのように捉え、どのように取り組み、どのように情報システムと連携させたのかを、実体験ベースで解説します。単なるマニュアル作成では終わらない“運用設計としての標準化”の本質に迫ります。
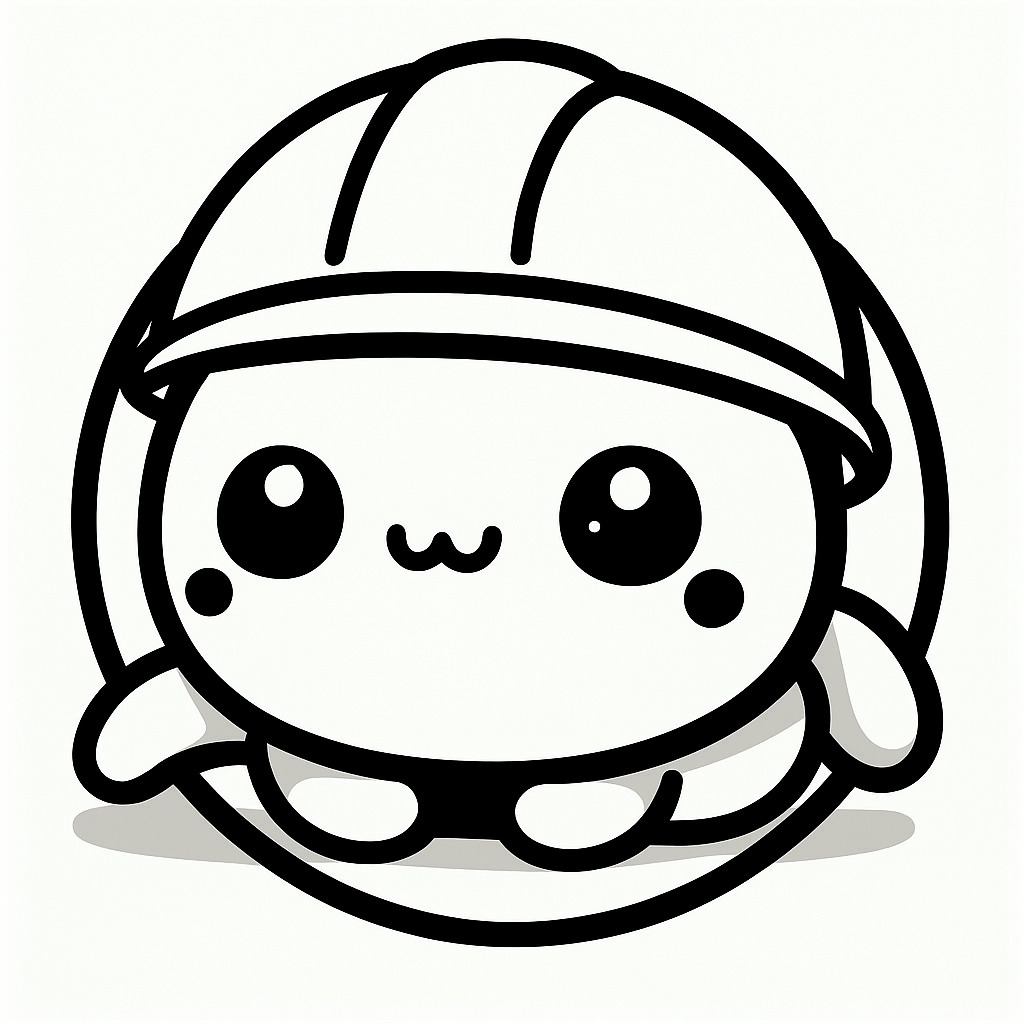
作業が“人に依存”してると、誰も悪くないのにミスになるんですよね…。標準化って、安心の基盤です😊
標準化の第一歩は“見える化”
最初にやったのは「誰が、いつ、どのように作業しているか」を一覧化することでした。作業時間・動線・作業者の手順メモ──あらゆる情報を時系列で記録し、Excelとホワイトボードで見えるようにしました。これにより、「作業者ごとの違い」が“数値”と“フロー”として浮き彫りになります。
なぜ手順が違うのかを対話する
作業の違いが“悪い”のではなく、そこには必ず理由があります。「自分はこの方が早い」「こっちの方が見やすい」。それらの“工夫”を全員で共有し、最も合理的な方法に集約することが標準化の肝です。現場にとって“押しつけ”でなく“選ばれた”手順にすることで、形骸化しないマニュアルになります。
システムは“間違えにくい設計”を
標準化された作業は、できるだけシステム側でもサポートするべきです。画面表示の順番を実際の動線に合わせたり、ピッキング画面を色付き+写真付きにするなど、“手順通りにしかできない”設計にすることで、新人や短期スタッフでも再現性が高くなります。
教育工数の削減とミス率の変化
標準化後は、教育時間が従来の半分に。ピッキングミス率も導入前の3分の1にまで減少しました。マニュアル+チェックシート+業務フロー図の三点セットを導入したことにより、誰でも同じ水準で作業できる環境が整ったのです。
まとめ:標準化は“無駄な差”を消すこと
標準化とは、「効率のよいベストなやり方を現場で共有し、誰でも再現できるようにすること」。作業者の工夫を集約して定着させることは、“熟練者にしかできない”を減らし、“誰でもできる”を増やすことです。
社内SEとしては、そのための記録・設計・補助ツール・UI改善を支える役割が求められます。人に依存しない仕組みこそ、持続可能な倉庫運用のカギだと、現場で強く感じました。
特に教育の観点から見ると、標準化は“教える側の負担”を減らし、“教わる側の不安”を減らす効果もあります。誰が教えても同じことを伝えられる。その安心感は現場の雰囲気にもつながり、離職率の改善にも貢献するケースがありました。
一方で、完璧な標準化は存在せず、現場の変化に応じてアップデートし続ける柔軟性も不可欠です。「標準化して終わり」ではなく、「標準をみんなで更新する」文化を作れるかどうかが、長く続く仕組みを支えます。
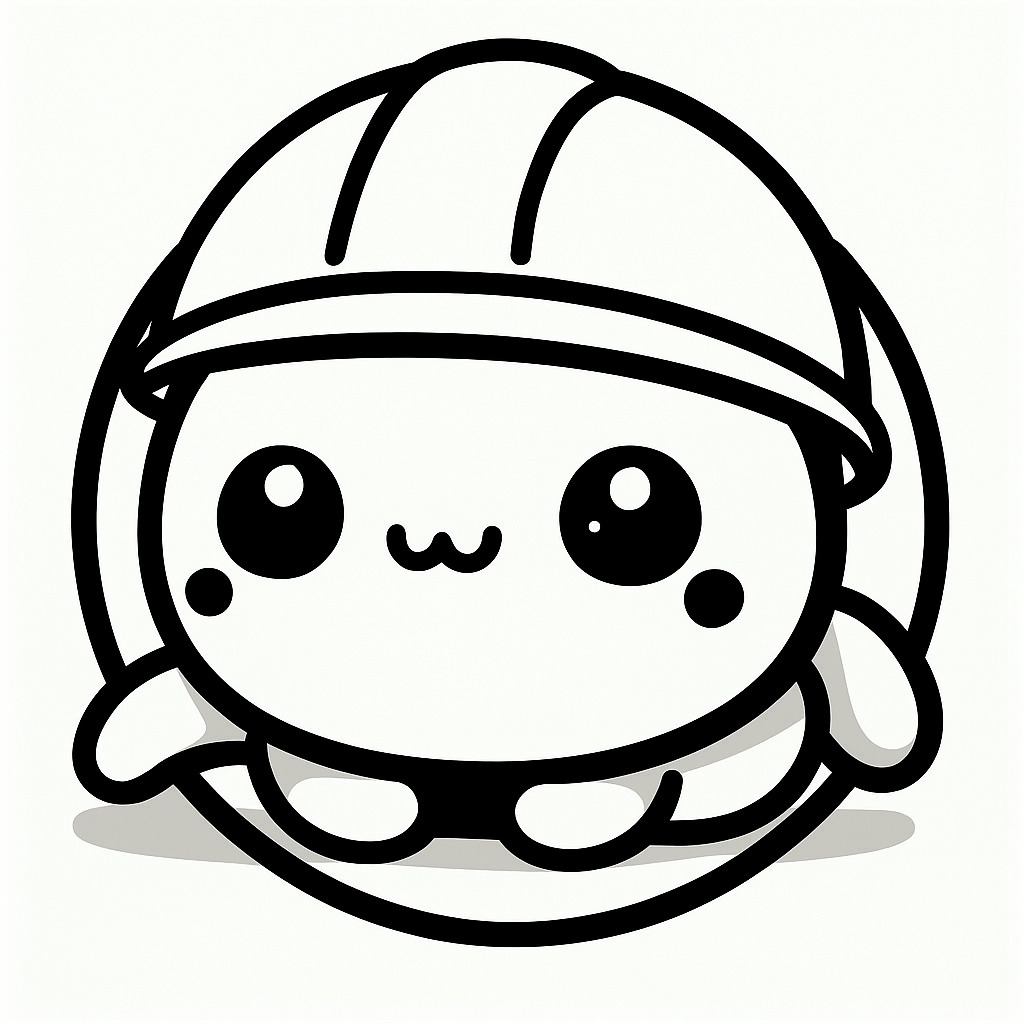
「誰でもできる」は、魔法じゃなくて工夫の積み重ねなんだなって気づきました…😊 標準化、ほんとに大事です!
コメント