はじめに
入荷・出荷・仕分け──物流現場において“紙ラベル”は今なお重要な役割を担っています。しかし、「ラベルを貼り間違えた」「印刷ミスで再発行」「貼ったけど読み取れない」など、紙ラベルを巡るトラブルは後を絶ちません。
この記事では、社内SEとして現場に紙ラベル運用の仕組みを導入した筆者が、「印刷→貼付→照合」までをいかに標準化・自動化・可視化したか、実例を交えて解説します。
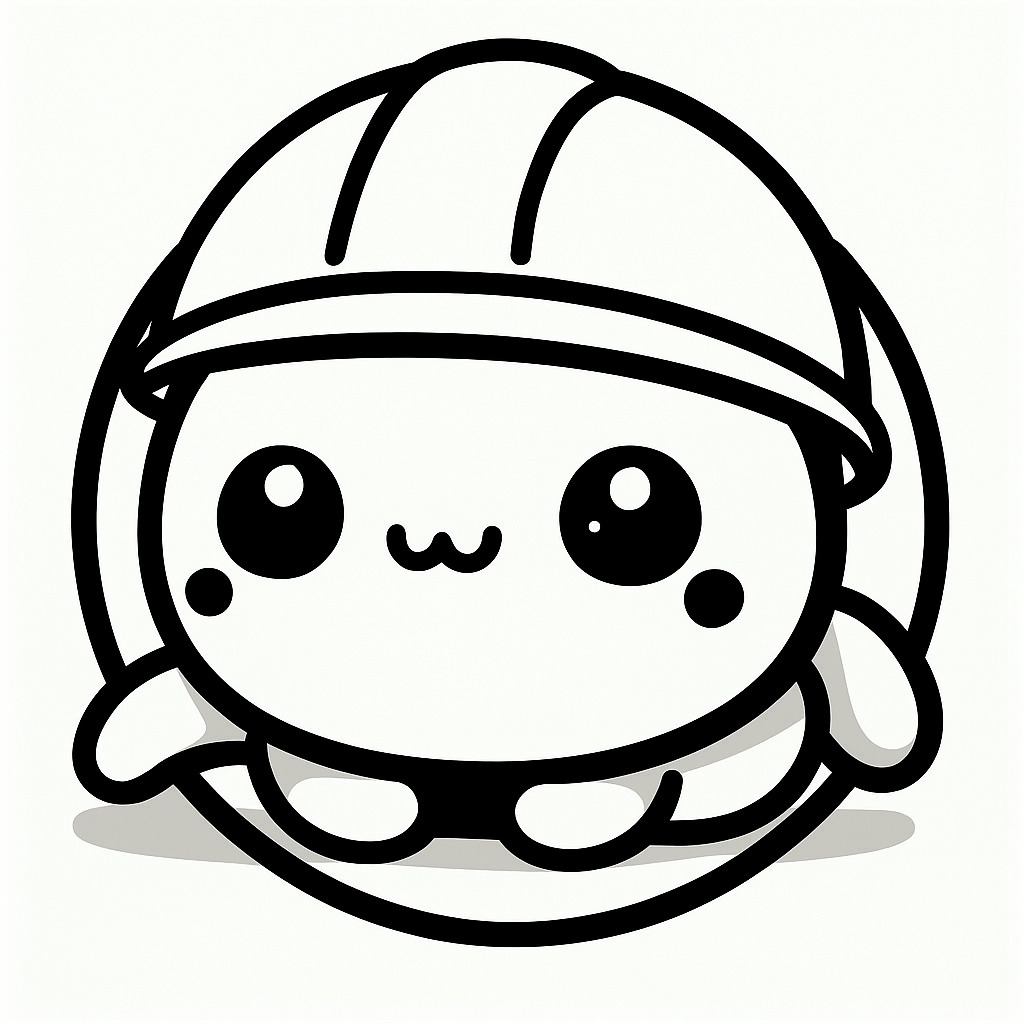
ラベルって「貼るだけ」に見えるけど、意外とヒューマンエラーが多いんです…!😊
事例①:印刷ミスと貼り間違いの多発
ある現場では、出荷時にラベルプリンタから大量印刷されたラベルが机に積まれ、「どれがどの商品かわからなくなった」という事態が頻発。結果、A社向けのラベルがB社の商品に貼られるなど、出荷ミスの原因となっていました。
私はこの状況に対し、以下の3つを実装しました:
- 出荷単位で1ロットずつ印刷を制御(ボタン1つで必要数のみ)
- ラベルに作業者名と時刻を印字(責任の明確化)
- WMSの画面に「ラベル印刷履歴」ボタンを追加し、再発行も履歴から選択
これにより印刷・貼付ミスは激減し、ラベル処理に関する問い合わせも3割以上削減されました。
事例②:照合ミスによる出荷トラブル
ラベルを貼った後、「本当にこの商品で合ってるのか?」が確認されず、誤出荷が発生するケースもありました。そこで私は、ラベルと商品に共通のバーコード(受注番号)を付け、貼付時に“Wスキャン照合”する方式を採用。
具体的には、商品ラベルをスキャン→続けて紙ラベルをスキャン→一致すれば「ピッ」と音が鳴る仕組み。違えば赤ランプ&警告音。シンプルながら、貼り間違いの大幅削減につながりました。
事例③:現場の貼りやすさにも配慮
意外な落とし穴だったのが、「ラベルが剥がしにくい」「貼る場所が決まっていない」といった“作業性”の問題。私は作業者とヒアリングしながら、「この商品は側面に、この商品は正面に」といった貼付ルールを明文化し、マニュアルに反映。
また、ラベル用紙をミシン目入りに変え、カットの手間を省いたことで、「ラベルが手間」という声も減少しました。
まとめ:ラベル設計は“仕組みと安心”のインターフェースである
紙ラベルは、ただ情報を印刷して貼るだけの存在に見えて、実は“現場オペレーションとシステムをつなぐ最後のインターフェース”です。ラベルがずれていれば出荷もずれ、ラベルが読めなければ商品も読めません。社内SEとしてこの領域に取り組むとき、求められるのは「正確な出力」だけでなく、「現場で迷わず貼れること」「照合できること」「再発行がすぐできること」といった、“人と工程にフィットする設計”です。
本記事で紹介したように、印刷履歴の可視化、照合スキャン、貼付位置の明確化など、小さな工夫の積み重ねがミスの未然防止につながります。そして、こうした仕組みの裏には、作業者の心理的不安を減らす“安心のデザイン”があります。人は、「これで合ってるのかな?」という不安を抱えながらでは集中できません。工程設計のなかで「確認できること」「間違えにくいこと」「責任が明確であること」が揃えば、作業はスムーズになり、自然と品質も上がります。
紙ラベル管理の改善とは、単に道具や手順を整えることではありません。それは“人・情報・工程をつなぐ橋を強くする”ことです。だからこそ、社内SEはシステムから現場までを見通し、「貼る」「読む」「安心する」までを一連の流れとして設計し続けなければなりません。ラベルという小さな紙片の中に、現場全体の信頼性と運用効率が詰まっている──その気づきが、次の改善のスタートラインになります。
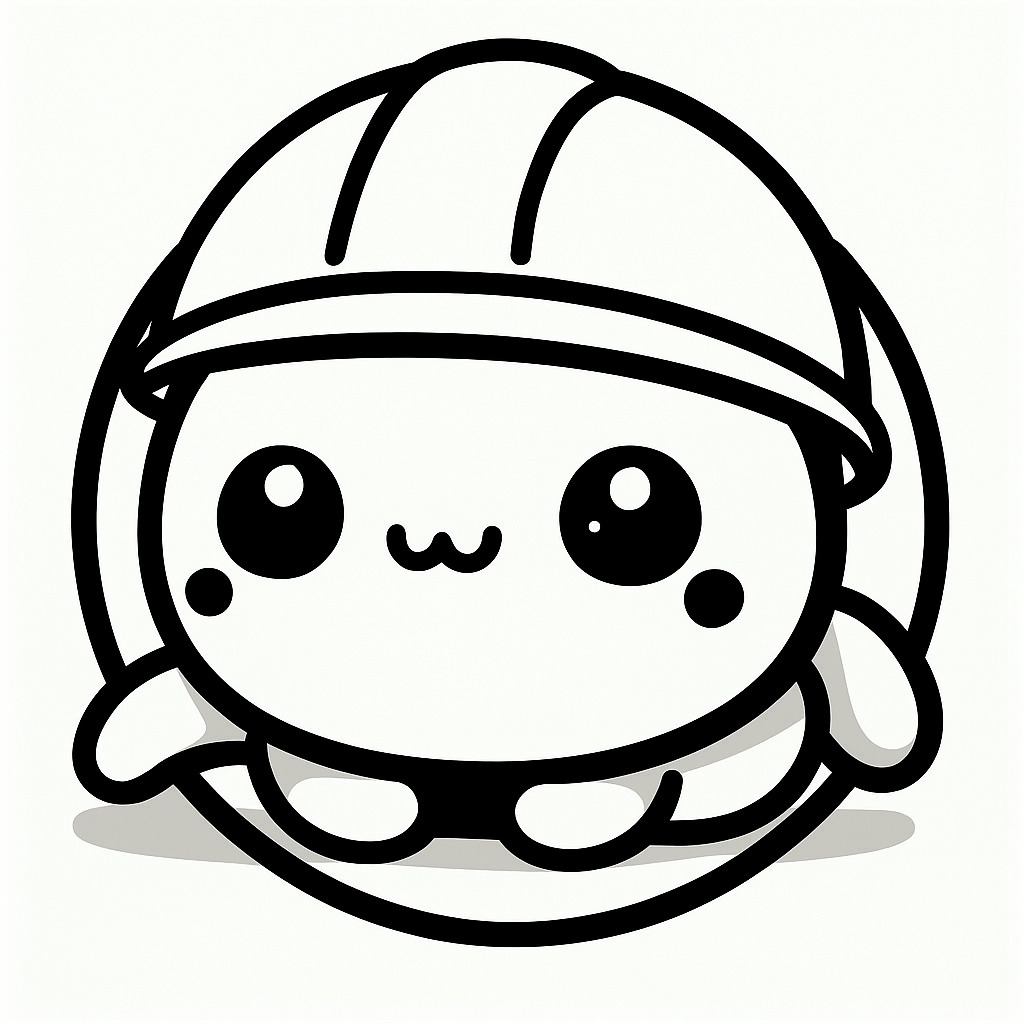
ラベルが「貼れる」ってだけじゃなくて、「貼りやすい・間違えない・安心できる」って大事なんですよね😊
コメント