はじめに
「なぜかいつも納期に間に合わない」「余裕を見ていたはずなのに遅れる」──そんな経験、物流や製造、サービス現場では日常茶飯事です。その原因の多くが、「リードタイム」の定義と把握が曖昧であることに起因しています。
この記事では、社内SEとして業務フローを分析し、リードタイムの“見えない要因”を特定・改善してきた事例をもとに、「なぜ遅れるのか?」の構造的な理由を具体的に解説します。
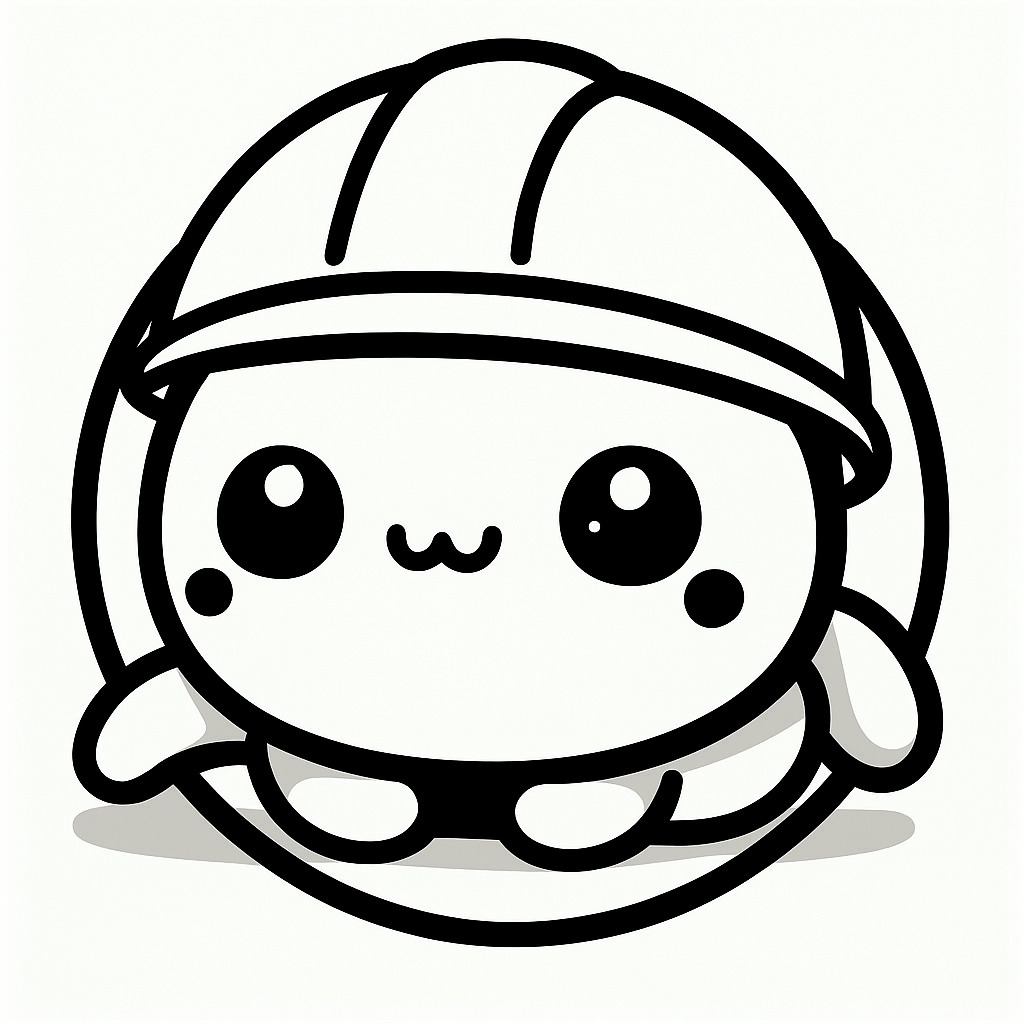
リードタイムって“何日かかるか”じゃなくて、“どこで詰まるか”を見つける道具でもあるんですね😊
事例①:出荷指示が午前中に出ない
ある現場では「当日出荷が間に合わない」と常に問題になっていました。ヒアリングの結果、システム上の出荷指示が9時には可能なはずなのに、実際には伝票出力が11時を過ぎていたことが判明。
原因は、営業部門の確認待ちや、朝の作業前ミーティングが終わるまで出力作業ができない運用が常態化していたことにありました。私は営業と物流の間にAPI連携を入れ、「9:00時点で入力されているデータを一括送信・ラベル自動印刷」する仕組みを導入。結果として出荷準備が2時間前倒しできました。
事例②:作業は終わっているのに報告が遅れる
製造業の現場でよくあるのが、「作業は終わっているのに、完了報告が遅くて次工程に移れない」パターン。実際には15時に作業終了しているのに、システム上では17時まで完了扱いにならない。
私はこのフローをタブレット入力+簡易な進捗ボタンに変更し、完了→報告のタイムラグを10分以内に短縮。さらに、「報告が一定時間されない場合に上長にLINE通知」という仕組みも加え、工程の“見えない隙間時間”をなくしました。
事例③:リードタイムに“移動時間”が含まれていなかった
ピッキング作業の遅れが発生している倉庫で調査したところ、「ピッキング→出荷場への移動」が平均8分もかかっていたにもかかわらず、WMS上ではその時間が無視されていたのです。
私は作業者の歩数と移動経路を記録し、「最も遠い棚を優先順に並べ替え」「一定以上の距離は事前アラート」といった導線設計を行いました。結果、1出荷あたりの総リードタイムが約6分短縮され、1日で合計1時間以上の作業削減につながりました。
まとめ:リードタイムは“遅れの正体”を可視化する道具
「リードタイムを短縮する」という言葉はよく使われますが、真に重要なのは「リードタイムを構成する要素を分解する」ことです。作業そのものだけでなく、待機・確認・移動・報告といった“周辺の工程”に多くのムダが潜んでいます。
社内SEとしては、それらを「時間」として記録・可視化し、再設計することが求められます。単に時間を測るのではなく、工程全体を“構造的に再定義”する視点が、リードタイムの改善には欠かせません。
また、工程のどこに“属人的な判断”が挟まっているかを見つけることで、自動化・標準化・先行通知といった仕組みを導入しやすくなります。リードタイムの見える化は、結果として“誰でもできる流れ”の実現にもつながるのです。
“なぜかいつも遅れる”──その原因は必ずあります。見落とされているだけです。それを可視化してあげることこそ、社内SEの役割だと私は考えています。
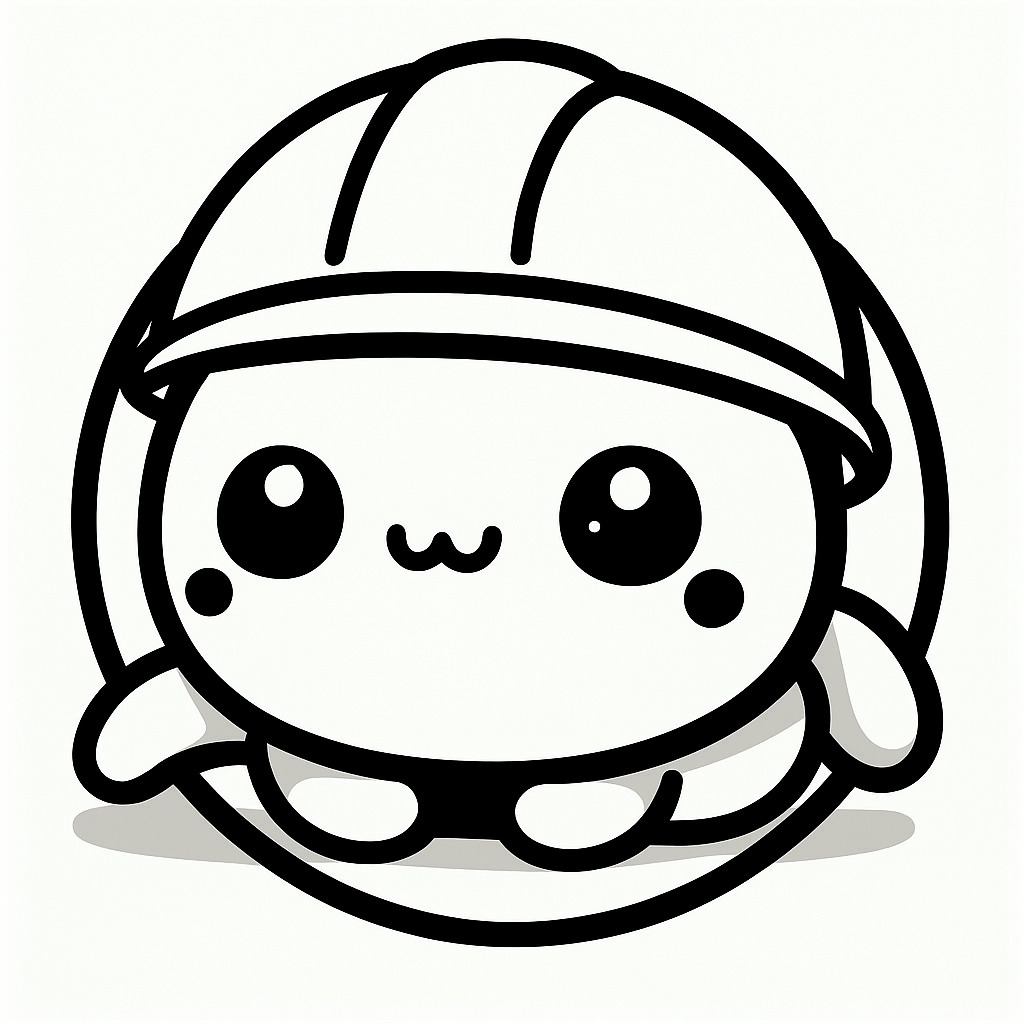
“なんとなく遅れる”は、ほとんどの場合“理由があるけど気づいてない”なんですよね😊
コメント