はじめに
「帳簿上は合っているのに、実際の在庫が合わない」「棚卸しのたびに誤差が出る」──このような“在庫ズレ”は、物流現場や倉庫運用で頻繁に起こる課題のひとつです。
その原因は「作業ミス」だけではありません。むしろ、見落とされがちなのが“記録”そのものの設計の弱さ。この記事では、社内SEとして現場に入り込み、実際に観察とヒアリングを重ねながら見つけた“在庫ズレの構造的原因”を具体例とともに解説します。
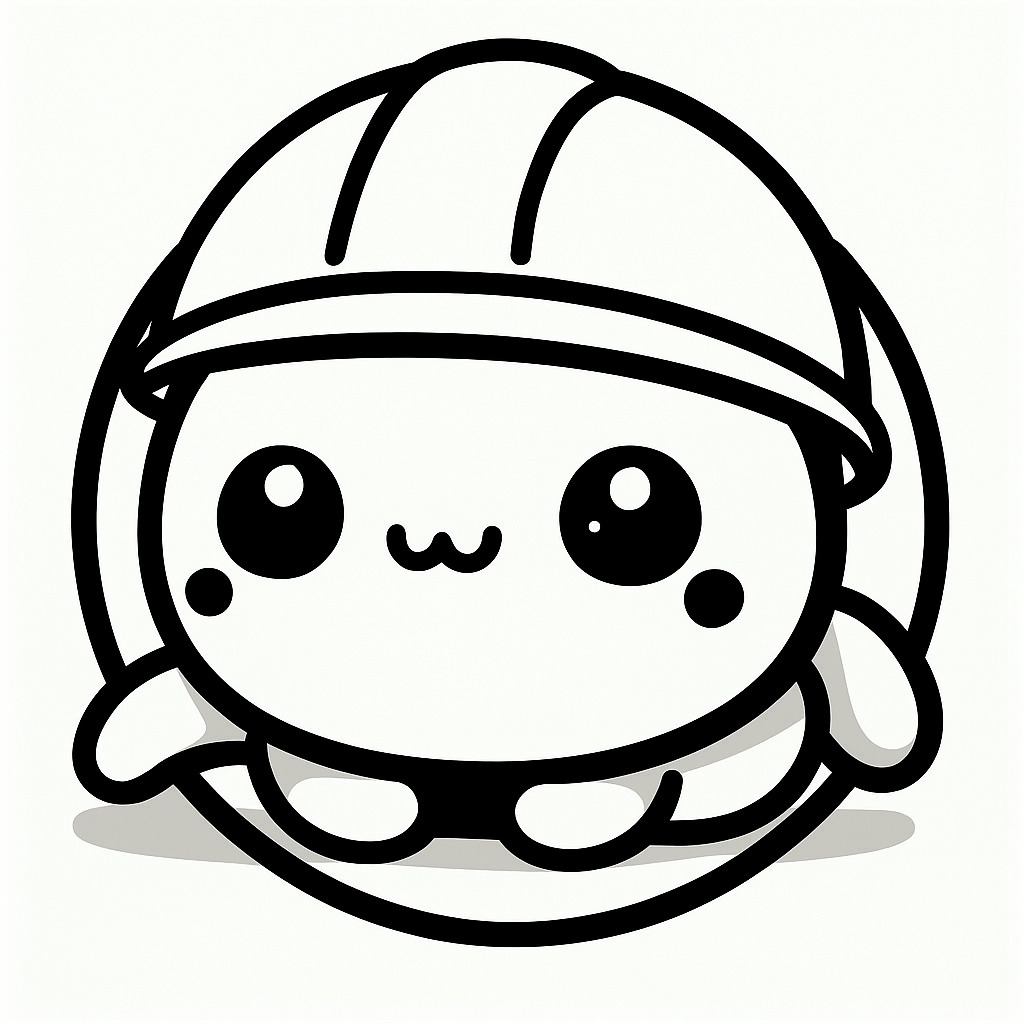
在庫ズレって、「誰かが間違えた」で片づけたくないんです。ちゃんと仕組みを見直せば、減らせるんですよ😊
事例①:ピッキング後の記録漏れ
ある現場では、在庫管理システム(WMS)で出庫記録が残らないまま商品が出荷され、棚卸しで大量のマイナス差異が発生していました。原因を探ると、WMSに「一括記録」ボタンがあるにもかかわらず、作業者が現場にタブレットを持ち込んでおらず、後からまとめて入力していたのです。
この「あとで入力」は、忙しさや退勤間際になると忘れられやすく、記録漏れにつながっていました。私は現場の導線に合わせて「棚横タブレット」を常設し、出庫後5分以内にその場で記録入力できるフローを再設計。結果、記録漏れは激減し、ズレが棚卸し前に修正されるようになりました。
事例②:仮置きエリアでのロケーション不一致
一時的に商品を仮置きするスペース──これは多くの現場に存在しますが、WMS上のロケーションを変えずに「とりあえず置いておく」ことがよくあります。結果、在庫上は棚にあるはずの商品が、実際は仮置きにあるという“ロケズレ”が発生。
私はこの仮置きエリアに特定のロケーションコードを付け、「仮置きは仮置きとして記録する」仕組みに変更。移動処理を簡素化し、画面に「仮置き商品一覧」が出るようにしたところ、棚卸し時に行方不明になるケースが激減しました。
事例③:返品・再入庫時の手順バラつき
返品された商品を再入庫する際、担当者によって「数量だけ増やす」「別ロットとして入れる」など対応がバラバラだったケースもありました。これにより「数は合ってるけど、場所やロットが違う」といった差異が多数発生していたのです。
私は返品対応用の専用画面を用意し、「返品理由・状態・再販可否」をラジオボタンで記録し、状態によってWMS側の登録処理が分岐するようにしました。これにより「記録方法のブレ」がなくなり、再入庫処理のミスがほぼゼロになりました。
まとめ:在庫ズレは“記録の構造”が原因
在庫ズレの原因は、単なる作業者の不注意ではなく、「記録のしくみ」「記録の導線」「記録ルールの曖昧さ」にあります。現場がミスを犯したのではなく、“ミスをしやすい環境”になっていることが本質なのです。
社内SEとしてできることは、操作の簡素化、記録の見える化、ミス防止のUI設計、そして運用ルールの明確化です。誰がやっても同じになるよう、作業の“構造”から見直す。それがズレの根絶に近づく一歩です。
また、「あとでやる」や「一括で処理する」といった“現場の暗黙ルール”があれば、まずはそれを言語化し、工程に組み込む必要があります。現場のリアルを知り、工程とデータを一致させることが何より重要です。
在庫ズレは、発生したあとに探すのではなく、「起きないように記録を設計する」こと。SEの立場から、それを支えることが真の改善です。
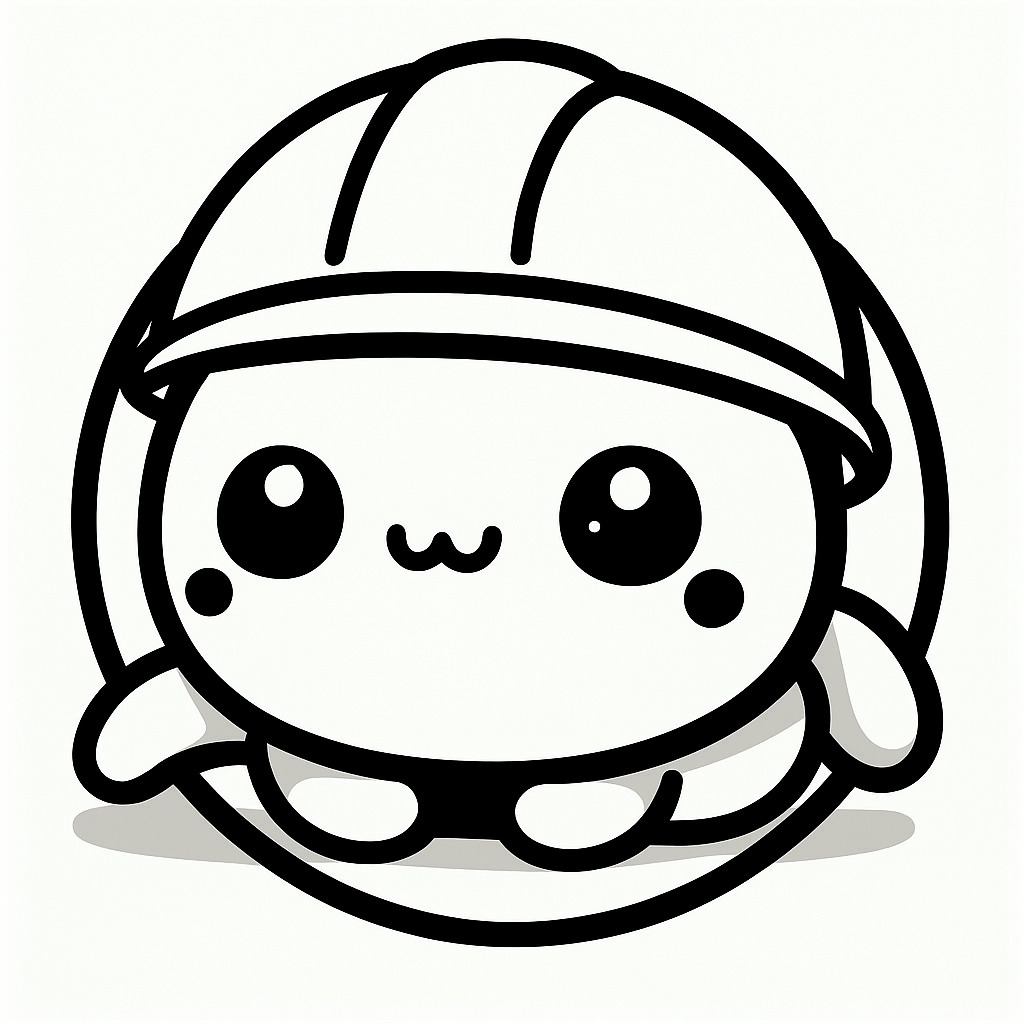
“ミスした人”を責めるより、“ミスが起きにくい仕組み”に変えていく方がずっと建設的ですよね😊
コメント