はじめに
物流現場の最初の工程──それが「入荷検品」です。どれだけシステムが洗練されていても、最初の工程が崩れると、そのあとのピッキング、出荷、在庫管理すべてに影響が及びます。つまり、入荷検品は“現場のスタートライン”であり、“エラーを発生させないための砦”でもあるのです。
この記事では、社内SEとして入荷検品に関わる中で気づいた「なぜ崩れるのか?」「どう立て直せるのか?」を、具体的な現場の事例を交えてご紹介します。
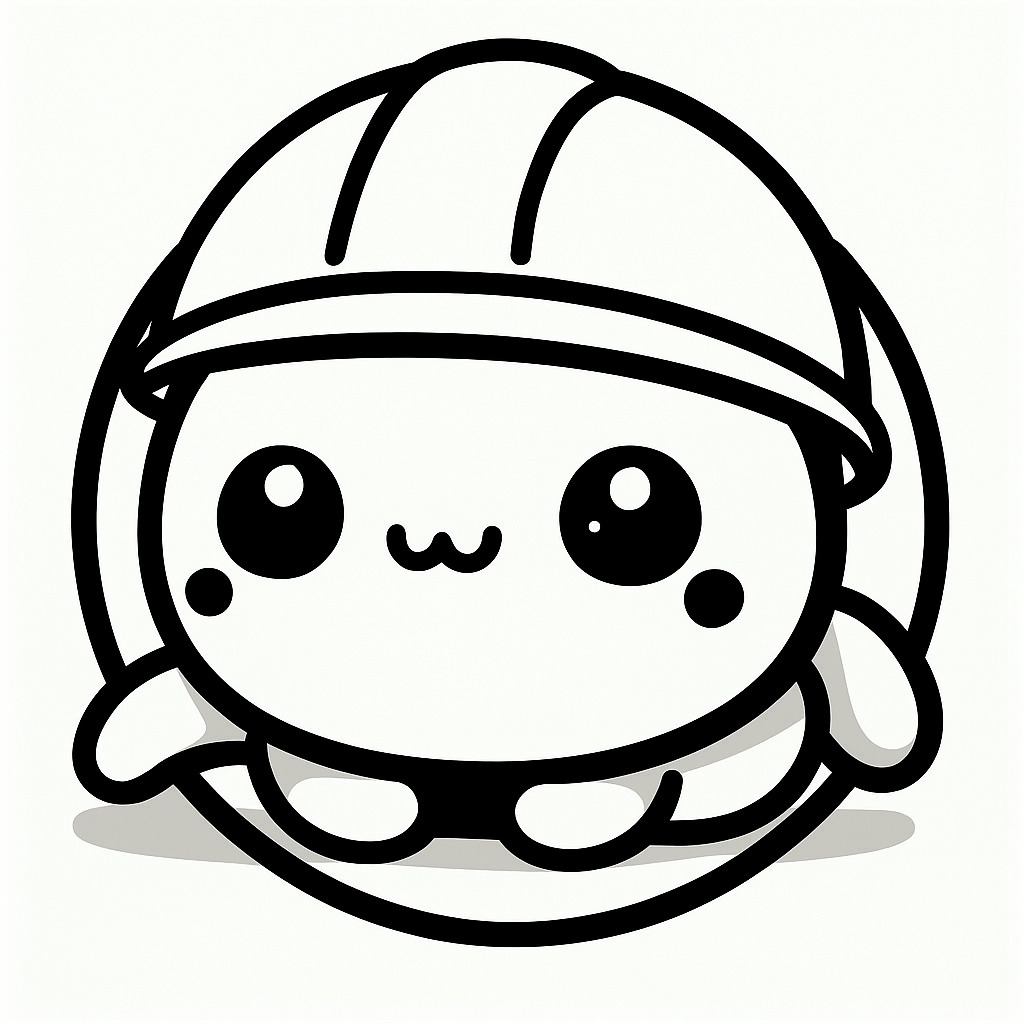
最初がズレると全部ズレる。だからこそ、入荷検品ってほんとに大事なんですよね😊
事例①:入荷リストの印刷漏れ → スキャン連携で即座に反映
入荷リストの印刷が間に合わず、現場が混乱するという“ありがち”なトラブル。紙のリストに頼っていた現場では、担当者が出勤してから印刷・仕分けという運用で、数分の遅れが検品全体を押し下げていました。
そこで私は、納品予定データをクラウドでリアルタイムに共有し、スマホやタブレットでスキャンできる簡易ビューアを構築。紙の印刷が間に合わなくても、スキャンですぐ確認できる環境にすることで、出勤直後のボトルネックを解消しました。
事例②:検品遅延 → チェックフローの“詰まり”を可視化
「入荷数が合っているか確認して」と言われても、何をどうチェックすればいいかが曖昧なまま進む現場。パートスタッフによって手順がバラバラになり、「全部見たつもり」が結果的に漏れに。
そこで、工程ごとの進捗をGoogleスプレッドシートで可視化し、「チェック済」「差異あり」「再確認中」のフラグをつけて運用。これにより、誰がどこで止まっているかが一目瞭然となり、リーダーがすぐにフォローに入れるようになりました。
事例③:ロット違いの混入 → アラートで事前防止
同一商品でもロットが違うと賞味期限や保管条件が変わるため、厳密な管理が必要ですが、現場では「見た目が一緒ならOK」として混入してしまうケースも。
私は、納品データの中に“ロット番号”を明示させ、それがシステム入力と一致しない場合はアラートが出る仕組みを追加しました。手入力の負担は増えましたが、「これ入れていいのかな?」という意識が根づき、混入トラブルが激減しました。
まとめ:「検品」は全体の安定性の礎
物流のすべては「正しい入荷」から始まります。検品のゆらぎは、そのまま在庫差異や出荷遅延に直結し、企業全体の信頼を揺るがすことにもなりかねません。
入荷検品という“地味な工程”ほど、標準化・見える化・エラー防止の仕組みを丁寧に積み上げることが、全体の生産性や顧客満足につながるのです。
社内SEの役割は、検品をただの作業ではなく“工程の基準点”として設計しなおすこと。人に依存せず、誰でも正しく処理できる仕組みをつくることで、現場全体の底上げが可能になります。
「早くやって」「合ってるはず」といった曖昧な指示ではなく、明文化された流れとフィードバックのある仕組み。それが、トラブルの芽を摘み、作業者の不安も減らします。
現場の声に耳を傾け、「わかってるつもり」を可視化し、「できてるつもり」をルール化する。そんなSEの視点が、検品工程における“仕組みの強度”を高めるのです。
検品は現場の入り口。だからこそ、そこを軽んじずに丁寧に設計し、支えることが物流全体の安定につながります。
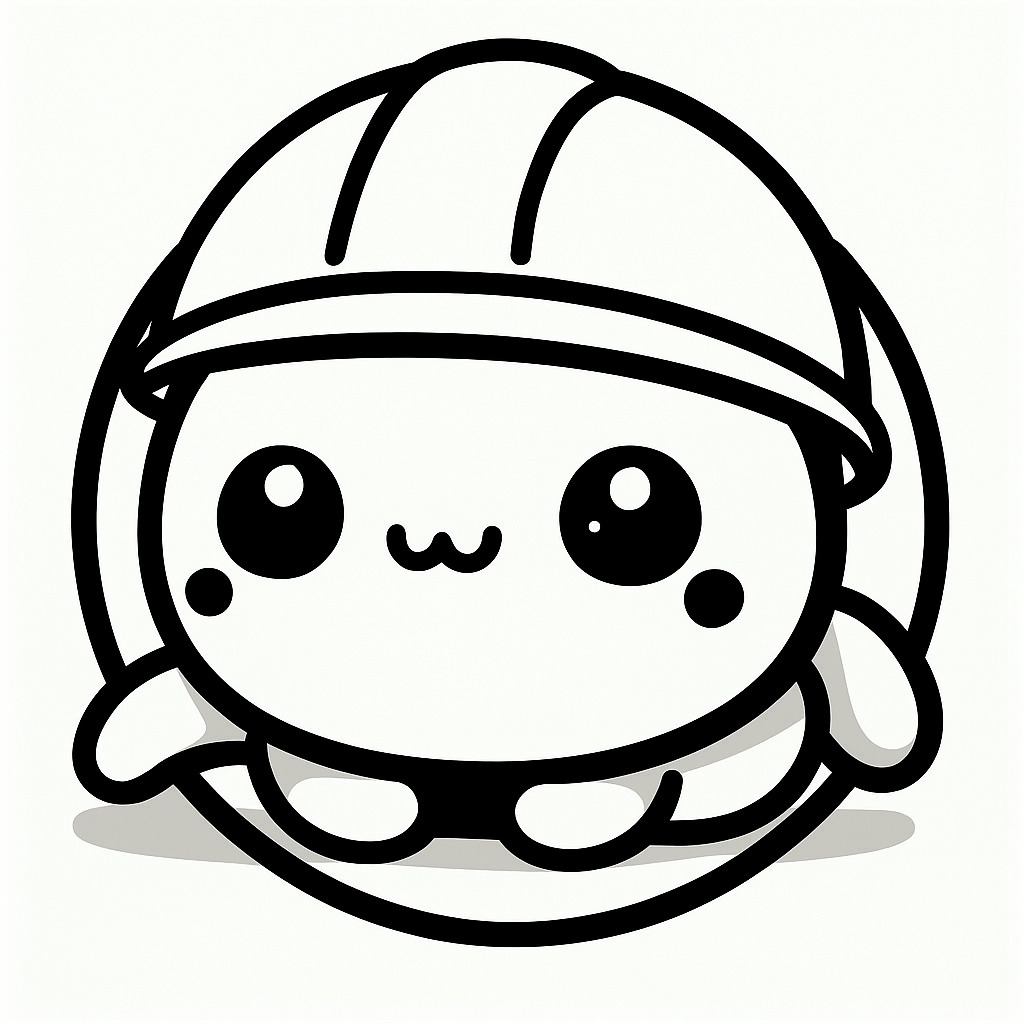
検品って、ほんとに地味だけど最強に重要な工程!見逃しがちな“入口”をもっと丁寧に見ていきましょう😊
コメント