はじめに
物流現場において、“ヒューマンエラー”は完全には避けられない課題です。スキャンミス、積み間違い、送り先の取り違え──こうしたミスは一見単純に見えて、実際には“工程のゆらぎ”が原因で発生しています。つまり、同じ作業でも人や時間、状況によって微妙にやり方が異なる。この“ゆらぎ”が、エラーを呼び込むスキマになるのです。
この記事では、社内SEの立場から、現場で繰り返されるミスにどう向き合い、どのように分析し、具体的にどんな対策を打っていったのか。単なるルール強化ではなく、“ゆらぎを許容しつつ、間違えにくくする”ための仕組みづくりの工夫をご紹介します。
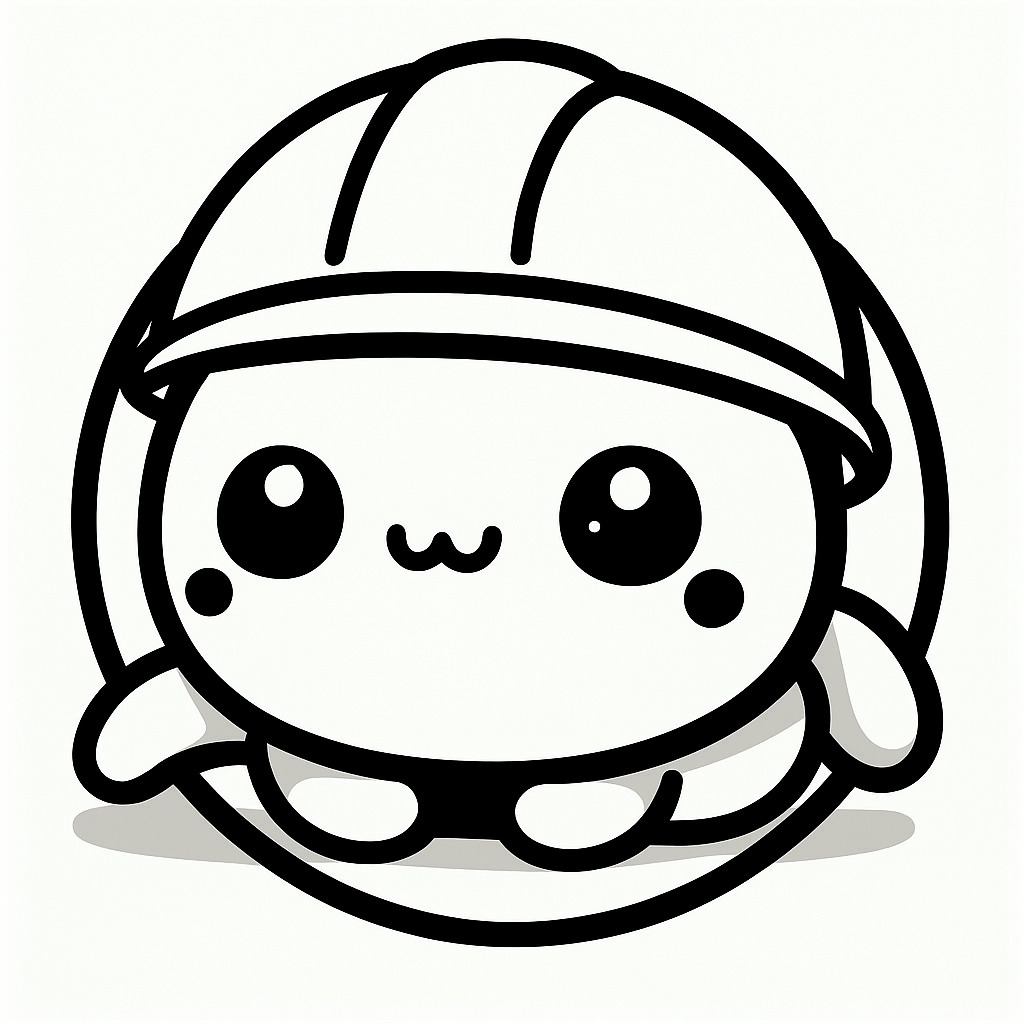
「また同じミス…」って、叱るより“仕組みで防ぐ”のがSEの出番ですね😊
なぜヒューマンエラーはなくならないのか
「マニュアルに書いてあるのに…」「教育はしたのに…」それでもミスは起こります。なぜか? それは、物流現場が常に“動的”であるからです。時間帯、人員構成、物量、作業環境によって、“正しくやる”ことの条件自体が揺らいでしまうのです。
つまり、ミスは個人の怠慢ではなく、“構造の結果”であることがほとんど。そこにこそ、SEが入り込める余地があります。
現場ヒアリングで見えてきた「ゆらぎ」の正体
私が取り組んだ倉庫では、定期的に送り状の取り違えが起こっていました。現場ヒアリングを進めると、「出荷順の急な変更」「荷札印刷が間に合わず手書き」「トラック到着の遅延で焦る」など、作業者にとっての“揺れ幅”が明らかに。
一つひとつは“想定内の変動”かもしれませんが、それが重なるとヒューマンエラーのリスクが跳ね上がります。
“ゆらぎ対策”のポイントと仕組み化の工夫
- 出荷順変更時のトリガーをWMSに組み込み、強制的に検品順を更新
- 荷札の二重発行禁止と、発行ログの自動記録
- 出荷締切時間を画面上に常時表示し、“焦り”を可視化で抑制
- ミスが起きたときの“再発防止プロンプト”をシステムに実装
こうした対策は、現場に“覚えさせる”のではなく、“忘れてもミスにならない”ようにするためのもの。これがシステムによるヒューマンエラー対策の本質です。
まとめ:ミスを防ぐのは“注意”じゃなく“設計”
ヒューマンエラーはゼロにはできません。しかし、“起こりにくくする”ことはできます。そしてその鍵は、「人の力に頼る」のではなく、「工程のゆらぎを見越した設計」にあります。
社内SEの仕事は、現場の声を聞き、構造を読み解き、“ゆらぎを見える形にして整える”こと。怒らずに、あきらめずに、仕組みで支える。それが現場に本当に求められている支援です。
ルールではなく流れを、精神論ではなく仕組みを──その視点の転換が、ミスの少ない現場を生み出す一歩となります。
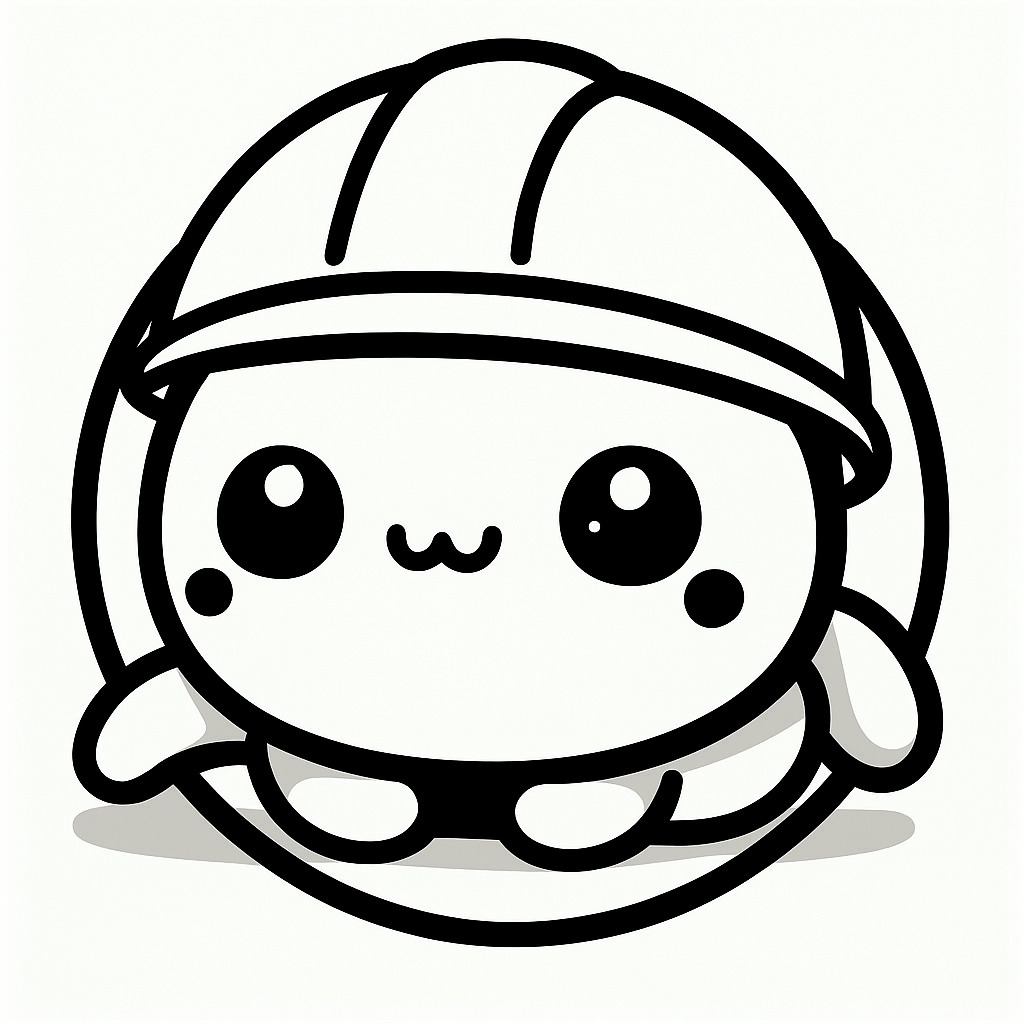
「人のせい」にせず「仕組みのせい」にする。SEって、現場にそういう安心感を届ける役でもあるんですよね😊
コメント