はじめに
「いつもどおり」が一番危ない──物流現場に関わるようになって、私が強く感じたことです。毎日繰り返す作業の中にこそ、思わぬ落とし穴があります。「慣れているから大丈夫」と思った瞬間にこそ、ミスや事故が起こる。この記事では、社内SEとして工程分析を行う中で見えてきた“慣れの構造的リスク”と、その対策について具体的な事例を交えてお伝えします。
習慣化された作業の中には、すでに“説明されていない手順”や“経験頼りの操作”が含まれていることが少なくありません。それが新人教育の障害になり、作業品質のばらつきを生み、時には大きな事故へとつながることもあるのです。
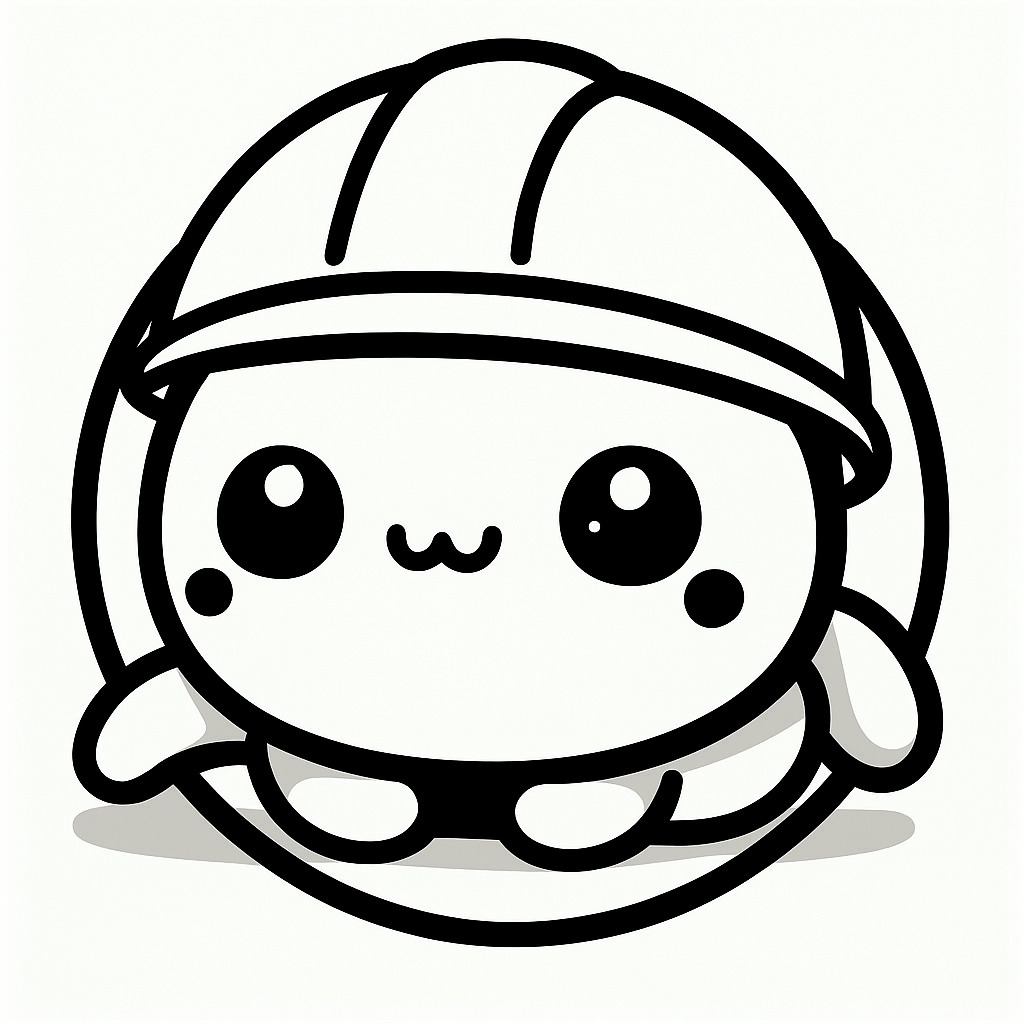
「いつもやってるから」って安心感、実は見落としの原因かも。だからこそ、見直す勇気が大事なんです😊
具体例①:出荷ラベル貼りミス
ある現場では、毎朝「商品に出荷ラベルを貼る」工程でトラブルが続いていました。手順は確立されているはずなのに、ラベルの貼り間違いや未貼付が頻発。調査の結果、原因は“慣れ”による作業の省略と判明しました。
ベテラン作業員は「この商品はいつもこの棚」「この棚の商品はあの店」と無意識に判断しており、確認手順を飛ばしていたのです。新人はそれを見て覚え、確認なしの手順が“いつもどおり”になっていたのでした。
具体例②:伝票番号の転記ミス
また別のケースでは、紙の伝票番号を管理システムに入力する工程で、番号の“桁抜け”や“上下逆”などの入力ミスが後を絶ちませんでした。確認者も「いつも大丈夫だから」とチェックをルーティンで流してしまい、ミスがスルーされてしまう事態が頻発しました。
そこに潜んでいたのは、“作業の形骸化”。「確認する」という工程は存在するものの、実際には“チェックするフリ”になっていたのです。
「慣れ」は構造的リスクを内包する
人は習慣に頼ることで認知リソースを節約しますが、それは裏を返せば「考えなくても手が動く」状態。つまり、“見ているつもりで見ていない”ことが発生しやすくなります。そしてこの“慣れ”は、教育にも影響します。
熟練者が「見ればわかるでしょ」と思っていることは、マニュアルに書かれないまま伝承され、属人化した「暗黙知」となります。これが結果として、ヒューマンエラーの温床になるのです。
対策:ルールの再言語化と再設計
私が行った対策は、「慣れた工程の再観察」と「再定義」でした。具体的には:
- 現場のベテラン作業者の手順を動画で記録
- 観察しながら“省略されている手順”を洗い出す
- その都度確認ポイントを明文化し、マニュアルと照合
- チェックリストの追加・現場ポスター化・声かけルール導入
これにより、作業工程に「一呼吸おく」意識を加えることができ、事故の件数は約40%減少しました。
まとめ:「慣れ」は排除するものではなく見直すもの
「慣れ」は悪ではありません。むしろ効率を支える重要な要素でもあります。しかし、そこに“見落とし”が潜んでいないか、“形式だけの手順”になっていないかを、定期的に見直すことが必要です。
社内SEの立場からは、「仕組みの中に見直しの余白を作る」「確認ポイントを構造化する」といった設計で、慣れとのバランスを取ることが求められます。
現場の“慣れ”をリスペクトしつつ、“いつもどおり”を一度立ち止まって見直す。それが、事故のない持続可能な現場づくりの第一歩だと私は思います。
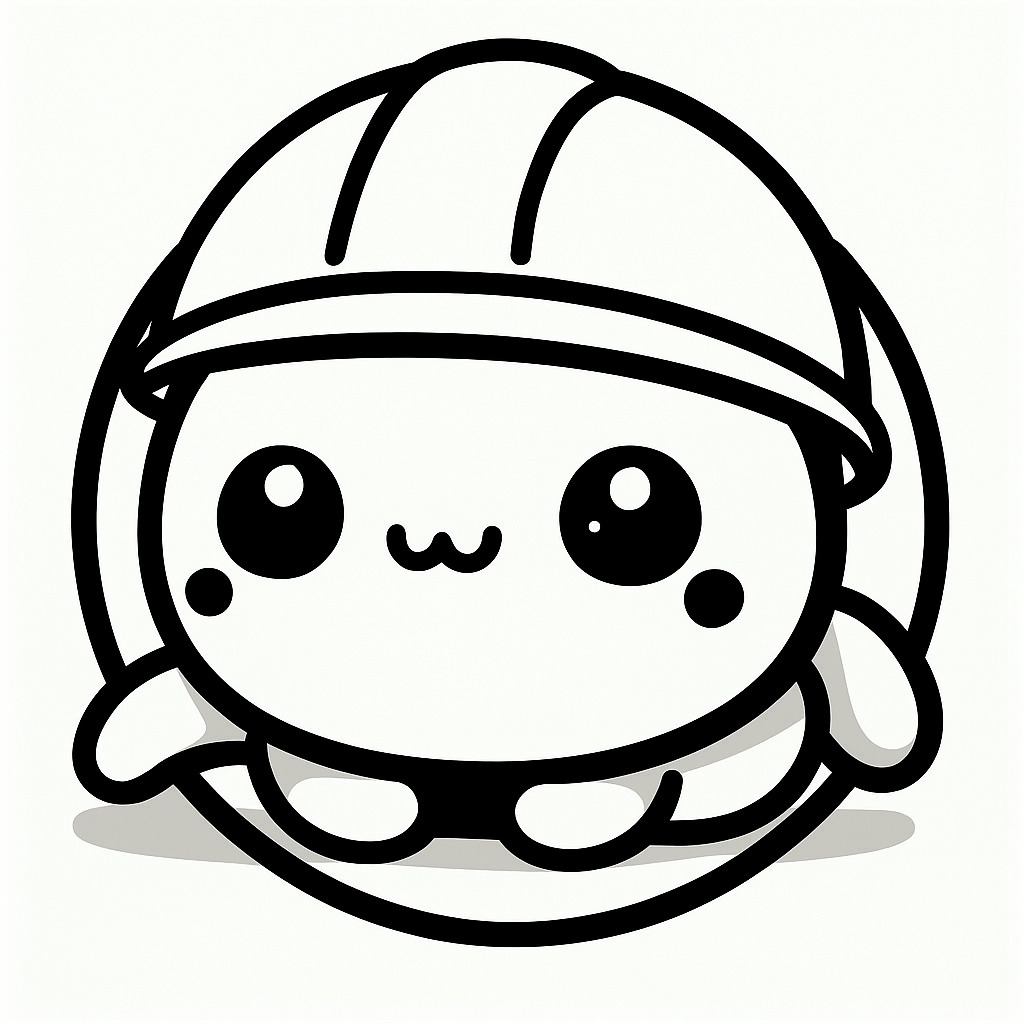
「いつもどおり」だからこそ、定期的に“見直す日”を作りたいですね😊 油断しない仕組み、大事です!
コメント