はじめに
「導線改善」と聞いても、ピンとこない人もいるかもしれません。ですが、物流や倉庫の現場では、“歩数と時間”こそが非効率のサイン。どれだけ作業を覚えても、動線が悪ければパフォーマンスは上がらず、ミスのリスクも高まります。実際、現場を観察してみると「AからBへ何度も往復している」「使わない棚を避けて遠回り」など、無意識の“ムダ”が多く存在しているのです。
この記事では、社内SEとして私が関わった導線改善の取り組みを紹介します。ポイントは、“感覚ではなくデータで見ること”。ストップウォッチと歩数カウンター、そしてExcelとスプレッドシートを使って「歩数と時間」を見える化し、どのように工程を整えていったのかを、実例とともにお届けします。
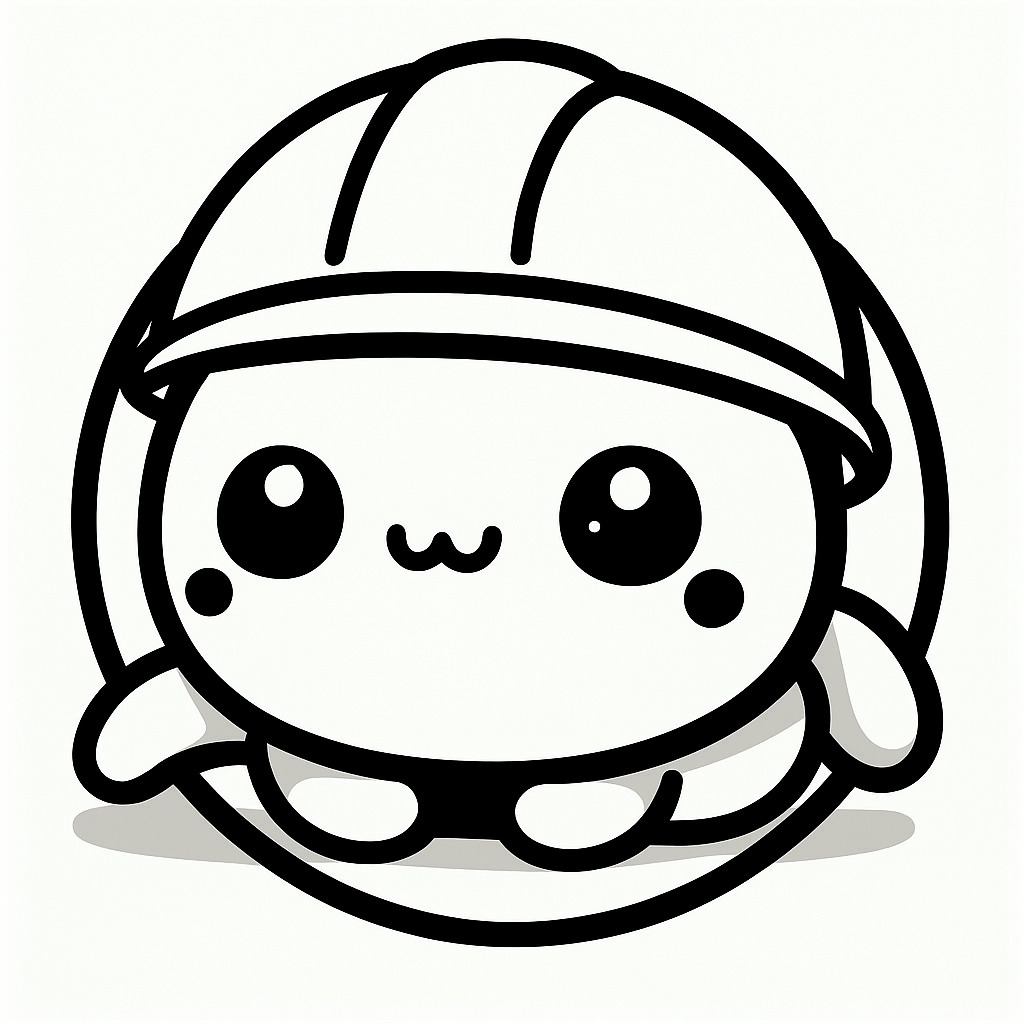
「慣れたやり方」って意外と遠回りなことも…!数字で見ると、見えてくるんですよね😊
実際の現場での測定方法
まずは現場作業の中から「ピッキング工程」を対象に選びました。1回のピッキングにかかる時間と歩数を記録し、作業ごとにExcelシートで記録。担当者別・ロケーション別の平均値を出すことで、「どこに差があるか」が見えてきます。
たとえば、ある作業員は1回のピッキングで平均280歩、別の作業員は180歩で済んでいました。差の100歩は「並べ方の違い」と「戻り動線の重複」から来ており、作業効率に最大で30%もの開きがありました。
改善に向けた可視化シートの工夫
計測結果をスプレッドシートでグラフ化し、「どのロケーションの導線が長いか」を一目で分かるようにしました。加えて、1ロケーション内での“回遊ルート”もレイアウト図にプロットし、「交差の多い動き」「無駄な往復」を線で表現。
この図を使って、現場スタッフと「どう並べれば短縮できるか」を話し合いながら改善案を出し、試験運用→再計測を数回繰り返して改善精度を高めていきました。
改善の結果と“見える変化”
導線改善の結果、歩数は約20〜30%削減、ピッキング時間は15〜20%短縮されました。さらに「迷わないように棚の番号と方向を大きく表示」「手元リストに地図つきロケーション表記を追加」など、視覚的な工夫も加えました。
これにより新人スタッフの教育時間も短縮され、定着率が向上。現場では「無意識に歩いてた距離って多かったんだな…」という声も聞かれ、改善に対する納得感が高まりました。
まとめ:数字で見るから納得できる導線改善
導線改善は、「感覚」や「経験」ではなく、「数値」で捉えることで初めて共有され、改善が進みます。歩数と時間という、誰にでも分かる指標に落とし込むことで、現場と一緒に改善を進められる土壌が生まれます。
社内SEの役割は、「変えること」ではなく「気づきを可視化すること」。そこに現場の納得が伴えば、改善は自然と広がっていきます。
一つの導線を短くすることは、作業者の身体的負担を減らすだけでなく、集中力や安全性の向上にもつながります。数字で見て、対話して、変えていく──それが、導線改善の本質です。
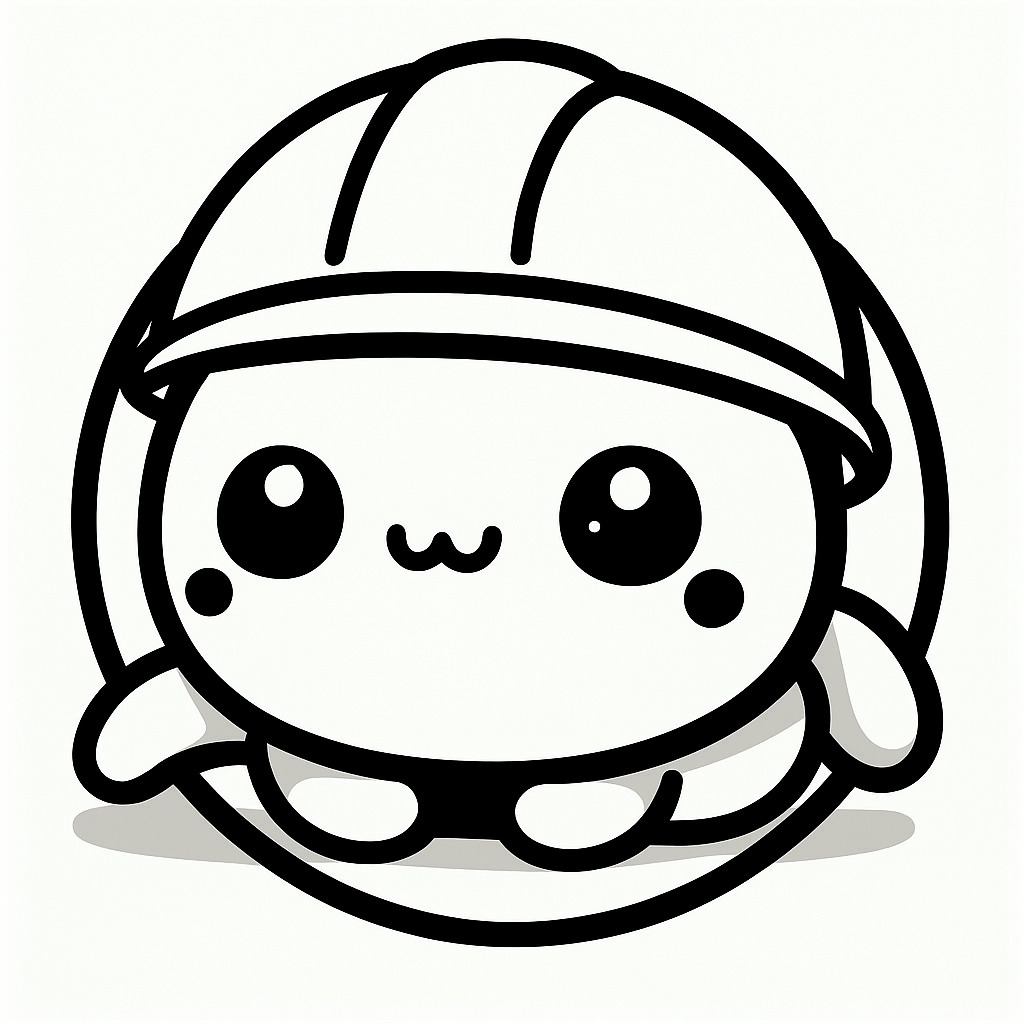
感覚に頼らず、数字で見る。シンプルだけど、すごく大事な一歩なんですよね😊
コメント