はじめに
飲料物流――それは「とにかく重くて早い」世界。ペットボトル、缶、ケース。とにかく単価が安く回転が速い。だけど重くてかさばる。さらに、配送先によってバラ積み・パレット・什器混載など要件はバラバラ。そんな複雑さとスピードを求められる現場に、社内SEとして飛び込んだときの衝撃は今でも忘れられません。
この記事では、私が飲料系3PLの倉庫管理システム(WMS)・配車支援ツール・実績収集フローの再構築に携わった経験をもとに、「重量×スピード×在庫最適化」がどう成り立っているのか、そしてその裏でSEがどう貢献できるのかをリアルにお伝えします。
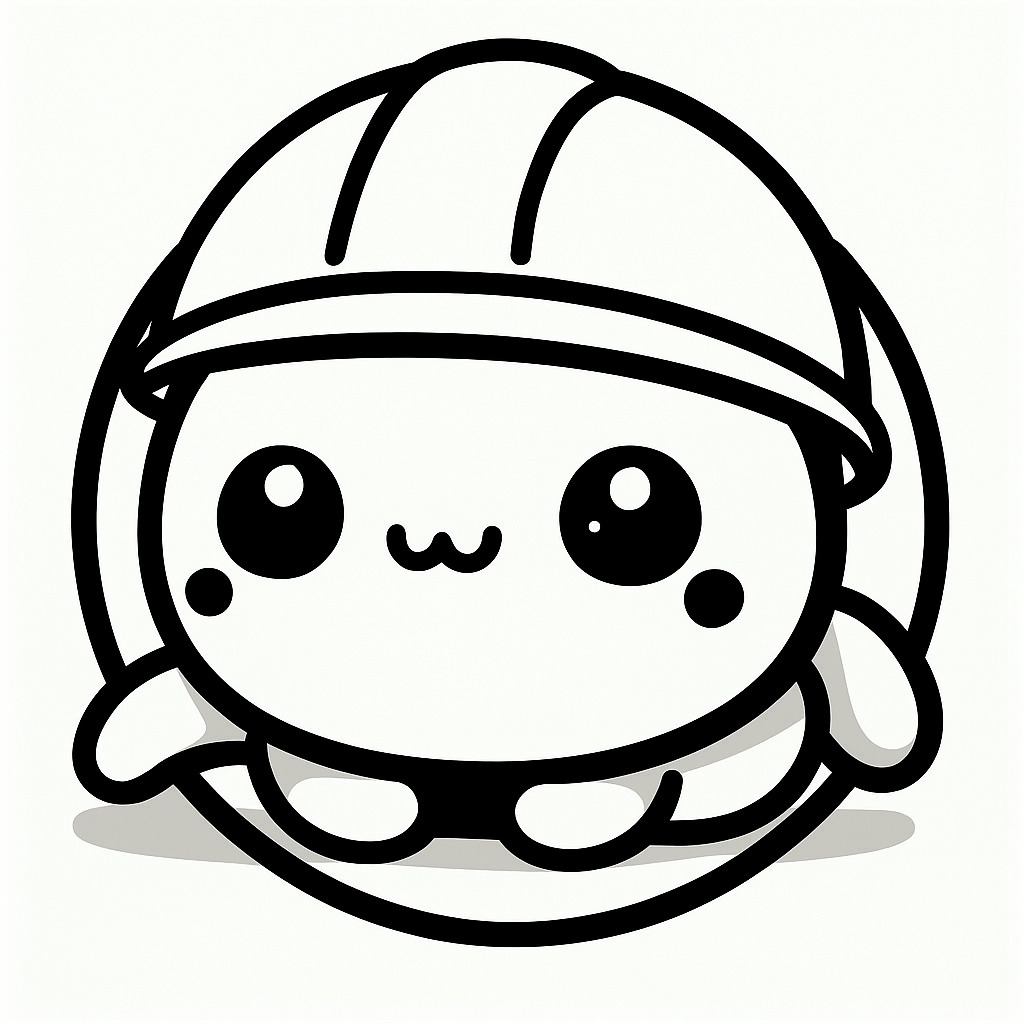
ケース単位で1トン超えもザラ!在庫って“重さ”なんだな〜って思い知らされました😅
“積めるかどうか”が在庫の境界
飲料物流では、「倉庫に入る量」より「出荷便に積めるか」が在庫の制約条件になります。500ml×24本ケースを100ケース、2Lペットのバラ品、販促用POP混載など、積載重量・容積・車両形状のすべてが影響します。出荷可能かは“物理的に積めるかどうか”に依存するのです。
スピード=時間ではなく“正解を早く出せるか”
出荷締切までに「最適なピッキング順」「積載効率の良い配車」「適正在庫」を即断する必要があります。SEとしては、過去データをもとに在庫シミュレーションや補充提案、ピッキング導線最適化を自動で出すアルゴリズムを構築することで、判断の“正しさ”と“早さ”の両立に貢献しました。
実績管理と在庫乖離のギャップ潰し
一番のトラブル要因は「帳簿上あるけど現物がない」在庫。特に飲料は重量物ゆえに崩れや破損が多く、現場での“勝手な差し引き”が常態化していました。SEとしては実績記録のシンプル化+例外時のコメント記録義務化により、「システム通りに動いてもらう」仕組みづくりを徹底しました。
まとめ:飲料物流は“工夫力”の総合戦
飲料3PLの世界では、「重さ」「速さ」「精度」が常にせめぎ合っています。現場作業の限界、在庫の動的変化、積載率と納品条件。すべてを見ながら判断できるのは人間だけですが、システムがその“正解に近づくための道筋”を整備することはできます。
SEが担うべきは、情報を現場の言葉に翻訳すること。そして現場の工夫をロジック化し、負荷を減らすこと。その積み重ねが、“地獄”と呼ばれるほど大変な飲料物流を少しずつラクにしていきます。
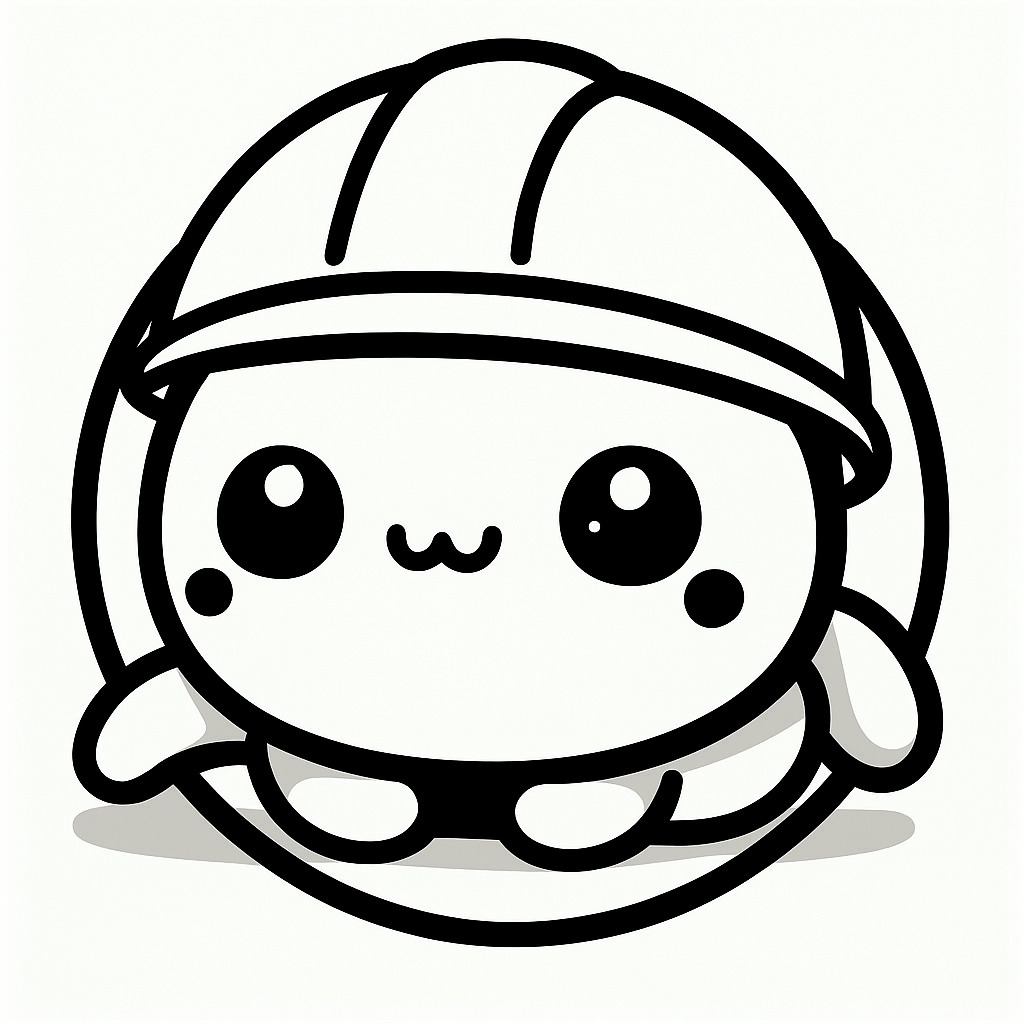
数字じゃなくて“物の重さ”で限界が決まるって、IT畑の人間には新鮮でした!現場のすごさに脱帽です…💦
コメント