はじめに
「5S活動って、ただの掃除でしょ?」──そう思っていた時期が、私にもありました。ところが、社内SEとして物流倉庫の業務改善に関わる中で、“片付けが組織の動きを変える瞬間”に立ち会ったことで、その認識が大きく変わったのです。
この記事では、5S(整理・整頓・清掃・清潔・躾)の本質的な意味と、業務改善の起点としての可能性、そして実際に社内でどのように取り組み、何が変わったのか──その具体的なプロセスと効果をお伝えします。
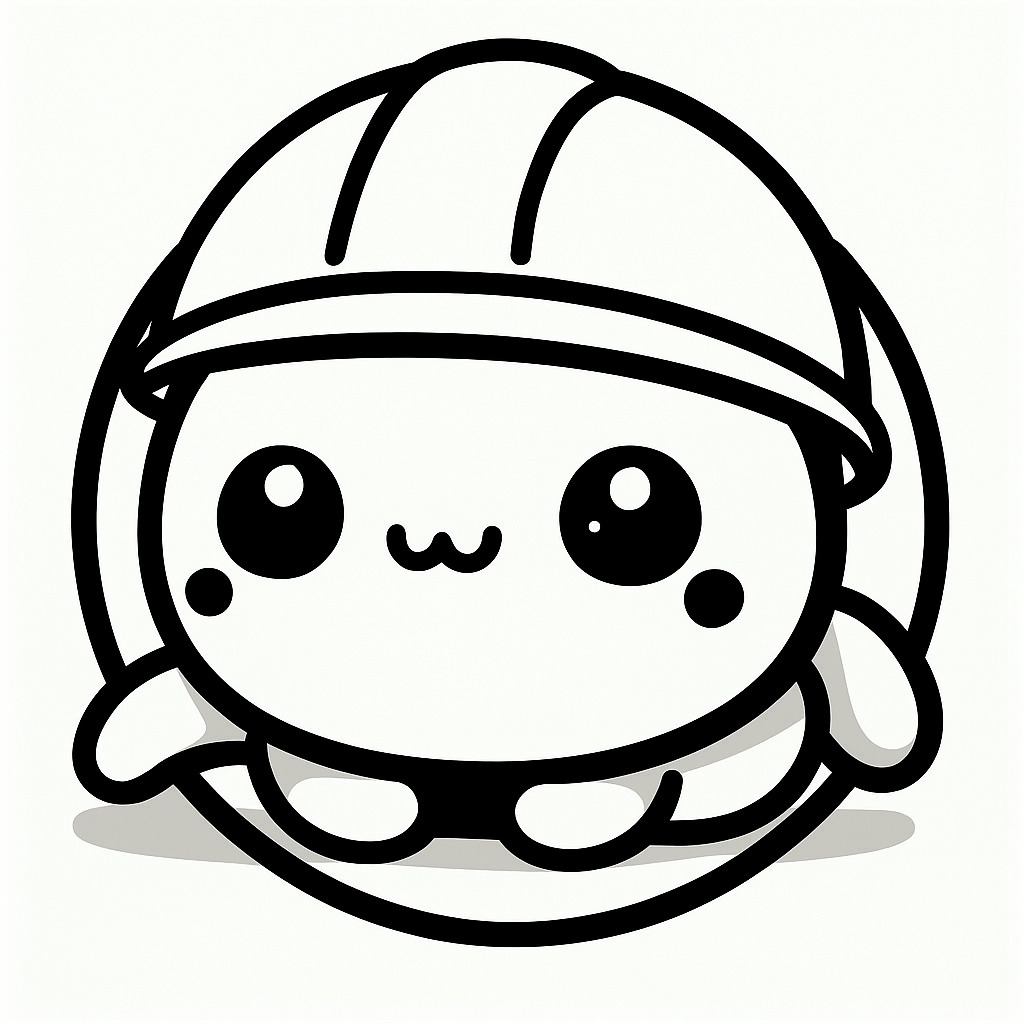
正直「掃除で何が変わるの?」って思ってたんです。でも、想像以上にすごかったんです…!😊
5S活動とは?基礎の整理
5Sは、次の5つの要素から成る職場改善の基本です:
- 整理:要るもの・要らないものを分ける
- 整頓:使うものを使いやすく並べる
- 清掃:掃除して常にきれいに保つ
- 清潔:整理・整頓・清掃を維持する
- 躾(しつけ):ルールを守り、習慣化する
これらは単なる美化活動ではなく、「ミスやロスを減らす」「異常をすぐに発見できる」ためのベースづくり。言い換えれば、“仕事の見える化”の入り口です。
事例①:道具の所在を明示しただけで作業効率30%UP
ある現場では、インパクトドライバーや梱包バンドなどの道具がバラバラに置かれており、使用後は「どこに返せばいいのか」が不明瞭でした。私は現場のリーダーと協力し、定位置ラベル+写真付き配置図を作成し、道具棚を再設計。
結果、「探す時間」がほぼゼロになり、1日あたりの作業スループットが30%改善。さらに、「戻す場所があると、戻したくなる」という声が複数の作業者から上がりました。
事例②:片付けが“異常の発見”を加速させた
別の拠点では、整理整頓が進んだことで、異常在庫や破損商品がすぐに目につくようになり、「いつからここにある?」「誰も気づいてなかった…」という状況が激減しました。
特に、棚下のスペースや隅のエリアに「明るさ・色分け・標識」を加えるだけで、放置物がすぐに見つかり、作業者の目線が変わっていく様子が見て取れました。
事例③:清掃が“工程のムダ”をあぶり出した
ある現場では、「毎日掃除をしているのに、毎日汚れる」という状況が続いていました。そこで清掃チェックシートに「汚れの出どころ」欄を追加し、汚れの場所と原因を可視化。
すると、汚れの原因が「パレット運搬時の段ボール破損」「ガムテープ屑の放置」などの“工程のムダ”にあることが分かり、作業フローの見直しにまで波及しました。
まとめ:5Sは“気づきの連鎖”を生む起点
5S活動は、たった1つの片付けから始まり、やがて“工程そのもの”や“人の動き”にまで影響を与える力を持っています。これは単なる整理整頓ではなく、仕事に対する視点と意識を変える文化づくりそのものです。
社内SEとして5Sに関わることで、「情報の見える化」だけでなく「物理空間の見える化」にも価値があることを痛感しました。紙の削減や棚番管理、作業ルールの明文化など、すべては“探さない”“迷わない”“比べられる”ための仕組みです。
そして、5Sは“誰でもできる”ように見えて、実は“みんなで続けないと意味がない”取り組みでもあります。ルールを破る人ではなく、守りたくなるルールを作ること。5S活動の真価は、そこにあるのだと思います。
さらに印象深かったのは、5S活動が“空気”を変えていったことです。倉庫の一角がきれいになり、ラベルが揃い、動線がスッキリするだけで、「なんだか気持ちいいね」という会話が自然と交わされるようになったのです。この“空気の変化”こそ、5Sの効果が見た目を超えて“意識”に作用している証だと感じました。
また、5Sが定着する現場では、“改善の土壌”も整います。道具の置き場所を変えると、「ついでにこの工程も見直したい」「あの帳票、手書きやめたい」といった声が現場から自然に出てくるのです。つまり5Sは、現場を“改善体質”に変えるスイッチなのです。
一方で、5Sが「やらされ感」になってしまうと逆効果です。現場が納得しないまま「ここにラベル貼ってください」「毎日清掃チェックしてください」と押しつけても、続かず形骸化していきます。だからこそ社内SEの立場からは、「ルールを守らせる仕組み」ではなく、「守りたくなる工夫」を重ねていくことが重要です。
最後にもう一度。5Sは“片付け”の話ではありません。仕組みを整え、情報と動作をつなげ、業務の中で当たり前にする──それが5Sの本質です。社内SEとしては「きれいにする」ではなく、「再現できる環境を作る」ことを目標にするべきだと私は感じました。
仕組みと文化の両輪で、現場の“やりやすさ”を引き出していく。それこそが、5SにおけるSEの役割ではないでしょうか。
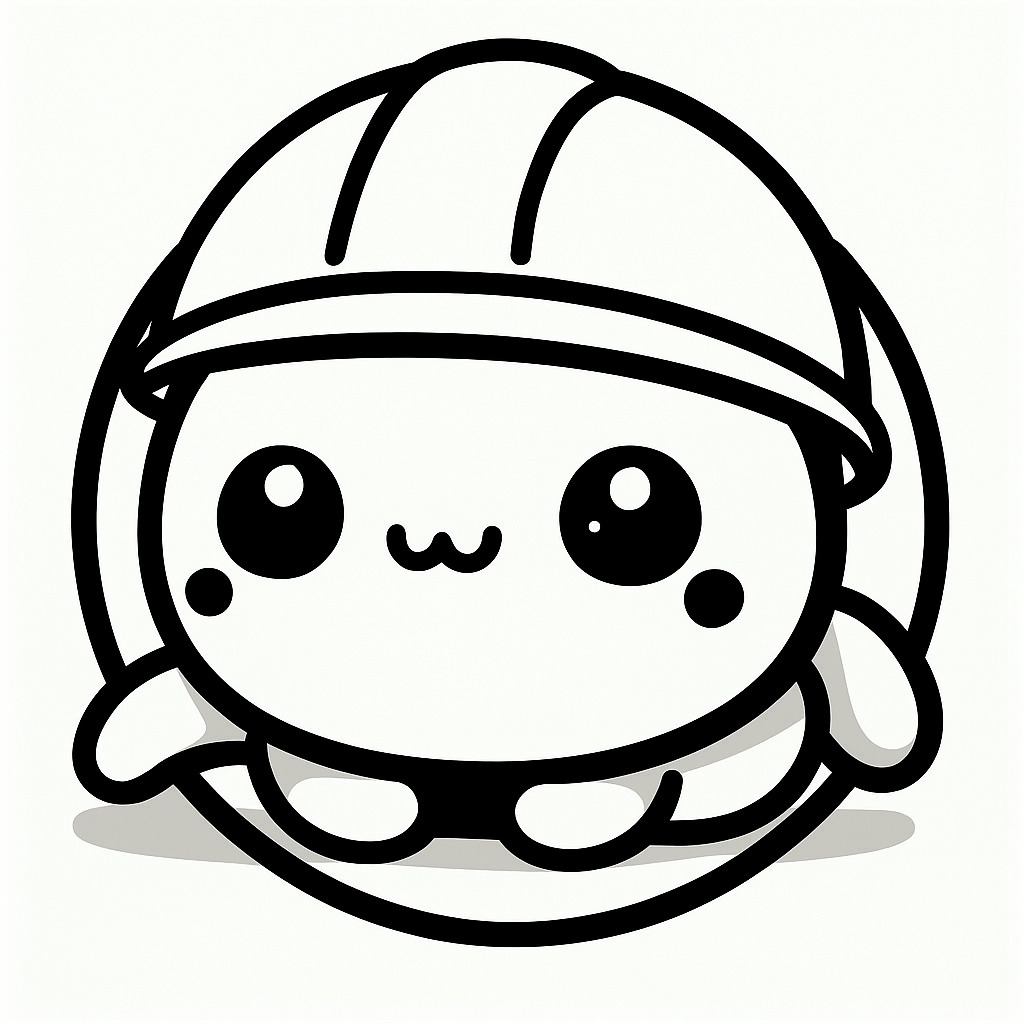
片付けって「めんどくさい」から始まって、「気持ちいい」に変わっていくんですよね😊
コメント