はじめに
「また出荷ミスか…でも原因がはっきりしない」──そんな現場の声に、覚えがある方も多いのではないでしょうか。作業ミスは、発生したその瞬間よりも、その“後の対応”で大きく差がつきます。
特に物流・製造の現場では、忙しい日常のなかでミスの記録や振り返りが後回しになり、「次にどう活かすか」が曖昧になりがちです。この記事では、社内SEの立場から「作業ミスをどう記録し、しくみに乗せていくか」について、実際の事例と工夫を交えて紹介します。
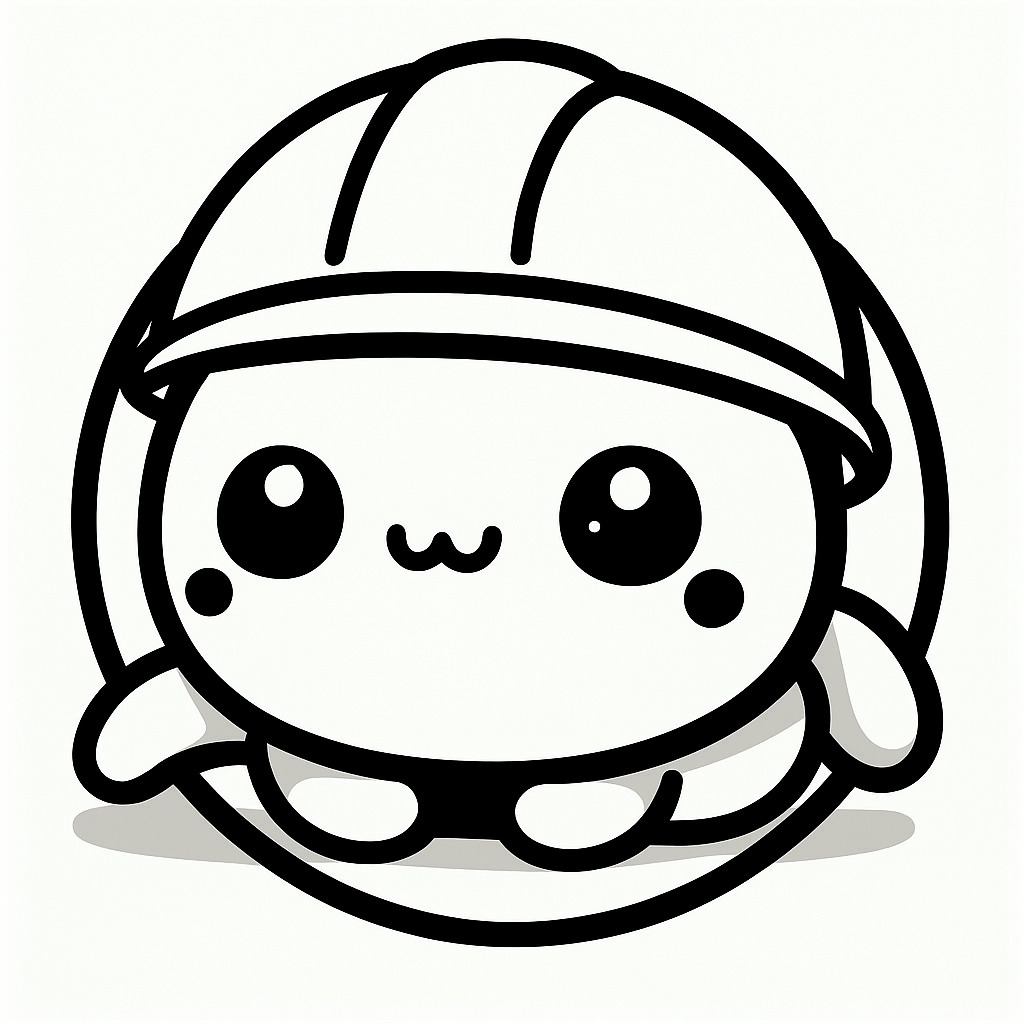
人のせいにしない“記録”って、ほんとに現場を変える力があるんですよ😊
なぜミスが“記録されない”のか?
そもそも、作業ミスの多くは“記録されていない”という問題から始まります。理由は単純で、記録する側にとって「面倒」「気まずい」「責任を問われるのが怖い」といった心理的なハードルがあるからです。
また、記録のフォーマットが複雑すぎたり、どこに書けばよいか分からなかったりといった運用面の問題もあります。こうして「記録されなかった失敗」が積み重なり、似たようなミスが繰り返されてしまうのです。
“隠されたミス”を拾い上げる仕組み
私がまず取り組んだのは、ミスの「報告しやすさ」を設計することでした。具体的には、Googleフォームをベースにした簡易な入力ページを作成し、次のような工夫を施しました:
- 匿名投稿OK(ただし端末IDで内部記録)
- 選択式のテンプレート化で入力ハードルを下げる
- 報告後に責められるのではなく、改善案の選択肢を提示
この仕組みを導入してから、月間ミス報告件数は3倍に増えました。ミスが増えたのではなく、「出てくるようになった」のです。ここからが、改善のスタートラインです。
事例①:ピッキング間違い→“棚ラベル見づらい”が原因
とある現場で頻発していたピッキングミス。報告フォームには「間違えました」のひと言しか書かれていませんでしたが、ヒアリングと現場確認で、“棚ラベルの印刷がかすれていた”ことが判明。誰も悪くない、でもミスは起きていた。
改善後、ラベルプリンタの定期メンテナンスを実施するようになり、同様のミスは大きく減少しました。ミスの本質は、記録の中に隠れています。
事例②:出荷伝票貼り間違い→“同じ品番が2列並んでいた”
作業者が出荷伝票を誤って貼りつけてしまい、別商品として出荷されたトラブル。原因は作業者の注意力ではなく、ロケーション設計にありました。2列連続で同じような品番が配置されており、視覚的に区別がつきづらかったのです。
私はロケーションの配列ルールを見直し、「似た品番は必ず1列空ける」ルールを導入。出荷前チェックシートもリデザインし、視覚的な誤認を防ぐしくみにしました。
“責任を追求しない記録”が改善を生む
多くのミス記録が消えていくのは、「誰がやったか」が問われる仕組みになっているからです。しかし、現場に必要なのは“責任の追及”ではなく、“再発防止の視点”です。
私は記録フォームの中に、「原因は?」「どうすれば防げる?」という選択肢を設け、記録=改善案という構造を作りました。これにより、「失敗しても書きやすい」文化が少しずつ根づきはじめました。
まとめ:記録は「責めない仕組み」であってこそ活きる
作業ミスの記録は、単なる“報告義務”ではありません。それは、現場の痛みを拾い、未来をつくるための入り口です。記録を集め、原因を探り、改善につなげる──そのプロセスを設計し、支えるのが社内SEの役割です。
記録を増やすためには、「書きやすさ」「責められない安心感」「改善につながる実感」が不可欠です。失敗は悪ではありません。見えないまま放置されることこそが、もっとも大きなリスクです。
だからこそ、作業ミスの記録は“攻めるため”ではなく、“支えるため”に使う。その視点を軸に、システムと人の橋渡し役を担うのが、社内SEの真の仕事ではないでしょうか。
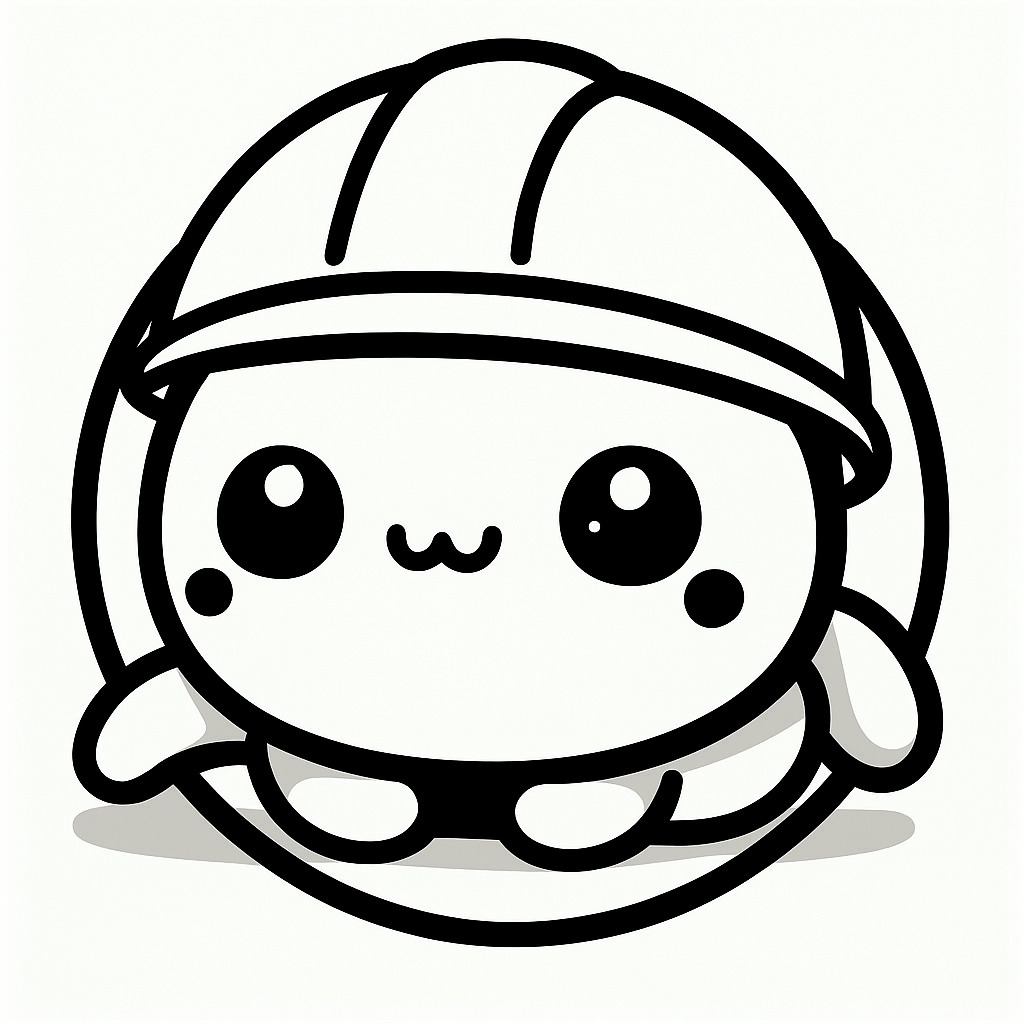
記録って“責める道具”じゃなくて、“直す道具”なんですよね😊
コメント