はじめに
「棚卸し」は、物流・小売・製造などあらゆる在庫を扱う業界で避けては通れない作業です。数量の実態とシステム上のデータを照合するこの作業は、単純に見えて非常に多くのリスクをはらんでいます。
この記事では、社内SEとして在庫差異に悩む現場を支援し、「どうやって棚卸し工程を整え、差異を減らしたか」について、実際に行った改善策を具体例とともにご紹介します。
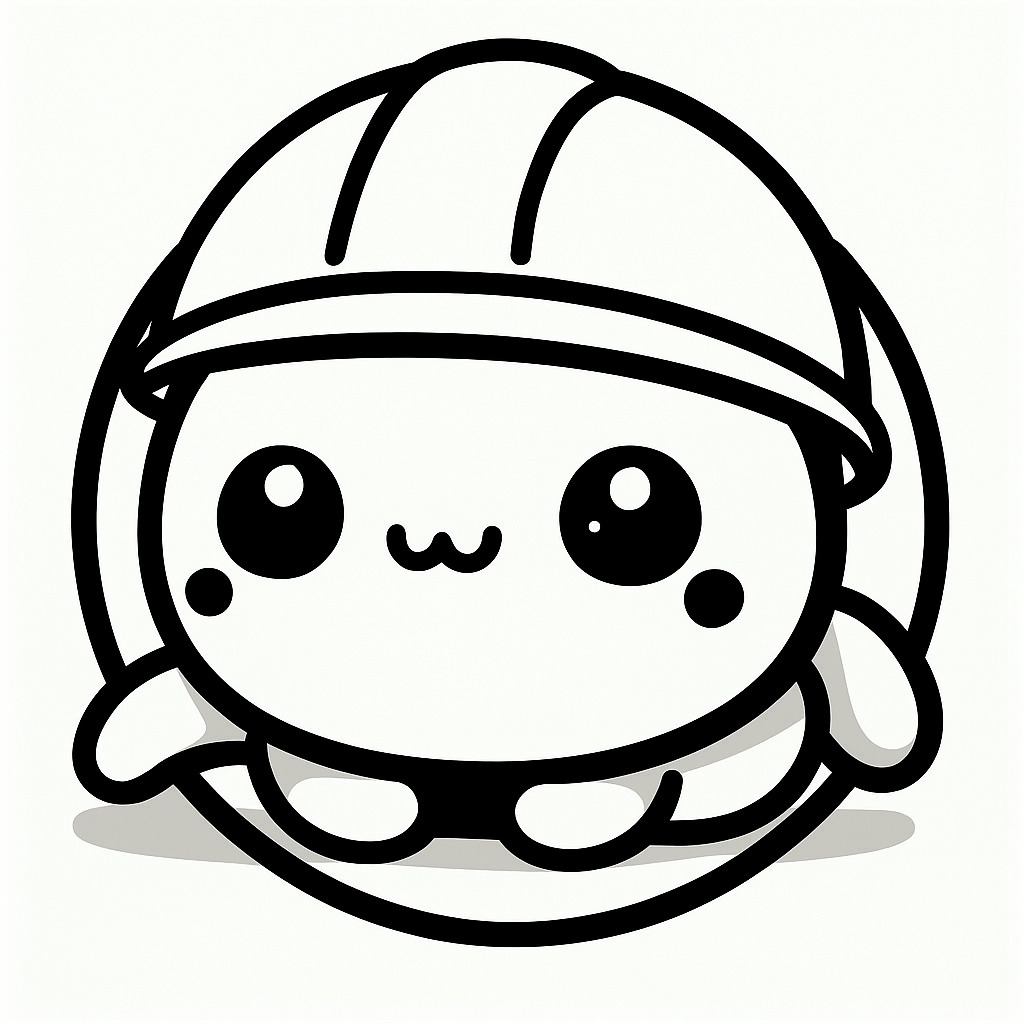
「棚卸しって、数字を数えるだけじゃないんだな」って、現場に入ってはじめて気づきました…😊
事例①:カウントミスが多発 → チェック方式を2段階に変更
ある倉庫では、年2回の棚卸しのたびに在庫差異が5%以上出ており、特に「人によって数え方が違う」「ラベルが読みづらい」といった理由で毎回やり直しが発生していました。
そこで私は、作業フローを次のように再設計しました:
- 棚ごとに2名体制(読み手と書き手)を固定
- ラベルを大判・太字に変更し、箱数確認欄を追加
- 1次チェック後に「棚卸し担当とは別の職員」がダブルチェックする仕組み
この結果、差異発生率は5%→1.2%まで減少。誤記がなくなり、精神的な緊張感も軽減され、「棚卸しが嫌じゃなくなった」との声も聞かれました。
事例②:紙記入の転記ミス → タブレット入力と写真記録
紙の棚卸表に手書きで数字を記入し、あとからExcelに転記する──この作業が属人化とミスの温床でした。とくに数字の読み違い(1と7など)が頻発しており、チェックのたびに差異が出る状態に。
改善策として導入したのが、タブレット端末による入力+現場写真の記録。フォームには「ロケーション」「SKU」「数量」を入力し、確認後に棚の写真を1枚撮影して送信。これにより、「現場の状況と記録をセットで残す」ことが可能になり、あいまいな報告が激減しました。
事例③:差異対応の混乱 → ログ記録の事前構築
棚卸しで差異が見つかったとき、誰がどこを見て、どんな操作をしたかがわからない──これが一番厄介な点でした。「きっと誰かがやった」ではなく、検証可能な状態を作ることが急務でした。
私は、入出庫の操作に簡易なログ記録をつけるよう改修し、たとえば「同じ商品が複数の棚にあった場合」「通常と異なる数を出庫した場合」などは赤字で表示されるようにしました。棚卸し時にはこのログと実数を照合し、「差異が起きた理由」が可視化されるようになりました。
まとめ:棚卸しは“制度”と“仕組み”で支える
棚卸しは単なる「数合わせ」ではありません。それは“在庫の信頼性”をつくるための、工程の集大成です。だからこそ、工程のどこか1つでも崩れると、差異が生まれ、現場は疲弊していきます。
社内SEとして重要なのは、「数えやすく」「間違えにくく」「記録に残る」仕組みを提供すること。作業者の努力に頼るのではなく、工程そのものを“事故の起きにくい構造”に変えることです。
また、棚卸し後の分析も改善のチャンスです。差異が出たロケーションはなぜ起きたのか?分類ミス?出庫記録?作業動線?──それを毎年振り返ることこそが、棚卸しの本当の価値です。
差異ゼロを目指すのではなく、「差異の理由が明確に説明できる」状態を目指す──それが現場とSEをつなぐ棚卸し改善の本質です。
最後に強調したいのは、「棚卸しは数える工程」ではなく、「信頼を再構築する儀式」だということです。現場とデータが一致する安心感。それを支えるのがSEの大事な役割です。
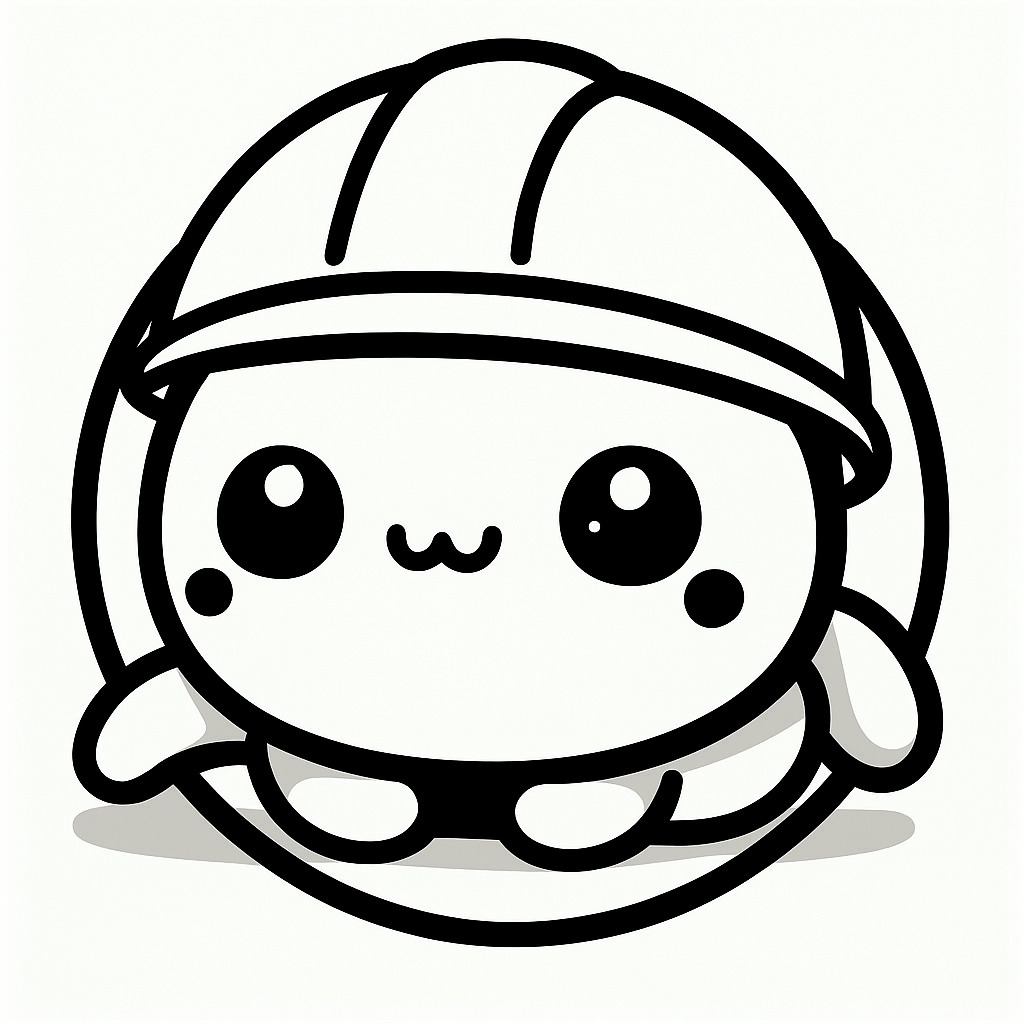
数字が“合う”だけじゃなくて、“納得できる”ことがいちばん大事なんですよね😊
コメント