はじめに
「積み残しが発生しました」──物流現場におけるこの一言は、配送計画や顧客満足に大きな影響を及ぼします。特に、積載量に余裕があるのに“うまく積めなかった”というケースは、社内SEとしても見過ごせない問題でした。
この記事では、積み残しの原因とその構造を掘り下げつつ、「載せられない」を防ぐ作業設計やしくみづくりについて、実例を交えて解説します。
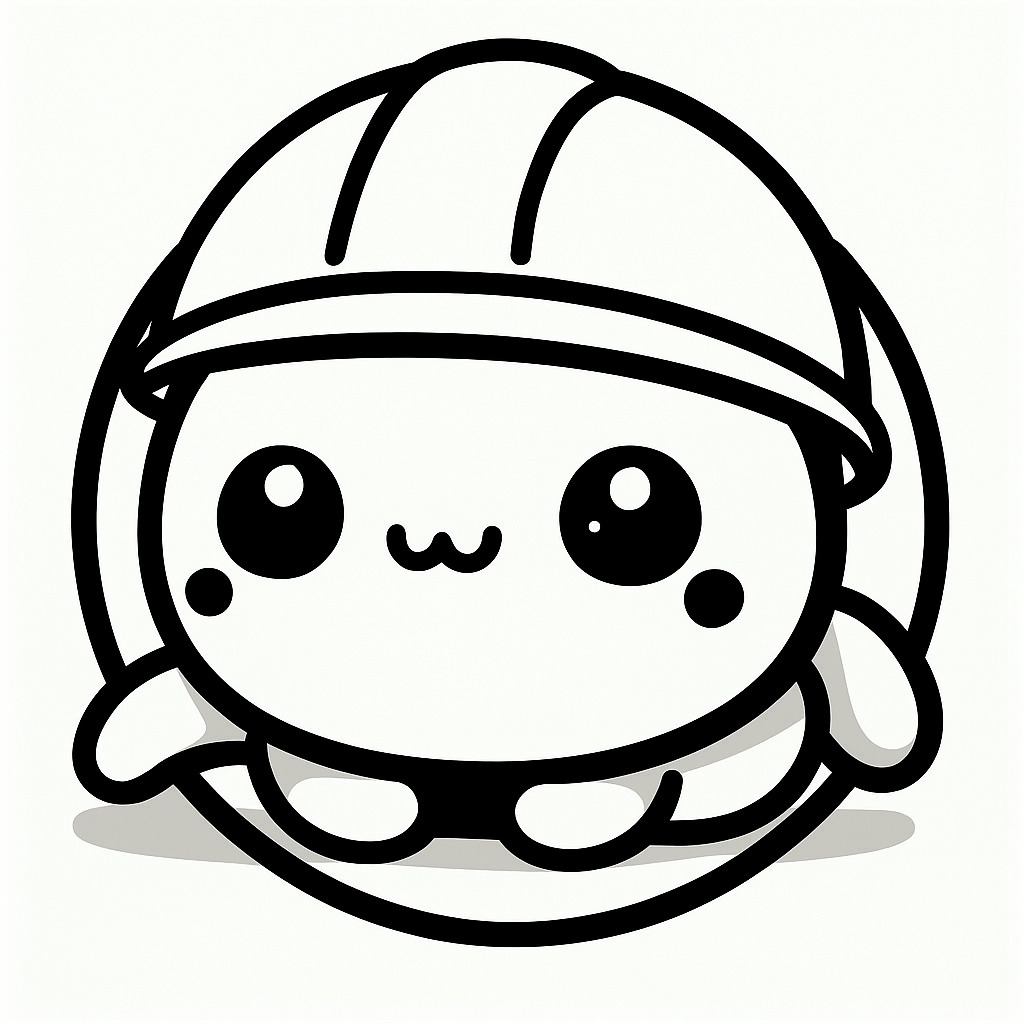
「空いてるのに載せられない」──最初は意味がわからなかったけど、現場にはちゃんと理由があるんですよね😅
積み残しとは?
積み残しとは、予定していた荷物を車両に積みきれずに残してしまうことを指します。これは単なる「積載量オーバー」だけでなく、「順番」「形状」「時間」などさまざまな要因で発生します。
問題なのは、車両にまだスペースがあるにも関わらず、荷物の形状や位置関係の都合で積めなかったという“見えない無駄”です。
事例①:段ボールサイズのバラつきが積載を崩す
ある出荷拠点では、大小さまざまなサイズの段ボールが混在しており、積み込み時にパズルのような状態に。途中で予定していた荷物が入らず、結局2便対応になってしまいました。
私は、段ボールサイズを3種類に統一し、積載シミュレーション表を現場で共有。結果として、積み残しがゼロになり、積込時間も20%短縮できました。
事例②:「後積み指示」が現場を混乱させた
ある日、クライアントから「この商品は最後に積んで」と突然の要望。ところが積込担当者はその指示を見落とし、結果として最終地点の荷物が手前に配置され、途中で取り出せず再配達に。
この反省をもとに、積込指示書に“積込順”の列を追加し、バーコードスキャン時に音声で「これは後積みです」と案内が出るように改善。指示ミスが激減しました。
事例③:積込作業の“時間配分”が原因に
一部現場では、「時間が足りず途中で作業終了し、残りは積めなかった」という積み残しが多発していました。原因は、積込時間の読み違いや、1人で全便対応していたこと。
私は積込スケジュールを分単位で見直し、「人数×便数」の作業負荷を可視化。繁忙時間帯は2名体制に切り替え、積み残しが大幅に減少しました。
まとめ:「積めない理由」に向き合う設計が必要
積み残しは単に“量が多すぎた”という話ではなく、現場の作業順、認識のズレ、ルール設計の甘さといった“見えない構造”によって引き起こされます。
社内SEとしては、これらを「現場のミス」と片付けるのではなく、「積めなかった構造」をひとつずつ解きほぐす視点が必要です。たとえば段ボールサイズの統一、積込手順の明文化、積載順の音声案内など、技術とオペレーションをつなぐ工夫が鍵となります。
また、“積み残しゼロ”を目指すことがゴールではありません。重要なのは、積み残しが発生したときに「なぜ?」「どうすれば次は避けられるか?」を現場と一緒に振り返る“しくみの再設計力”です。
積めなかった事実を“無理やり積む”方向で押し切るのではなく、「載せられる仕組み」「迷わない現場」を育てること。これこそが、積み残しを減らす本質的なアプローチであり、社内SEとしての価値を発揮するポイントだと私は考えます。
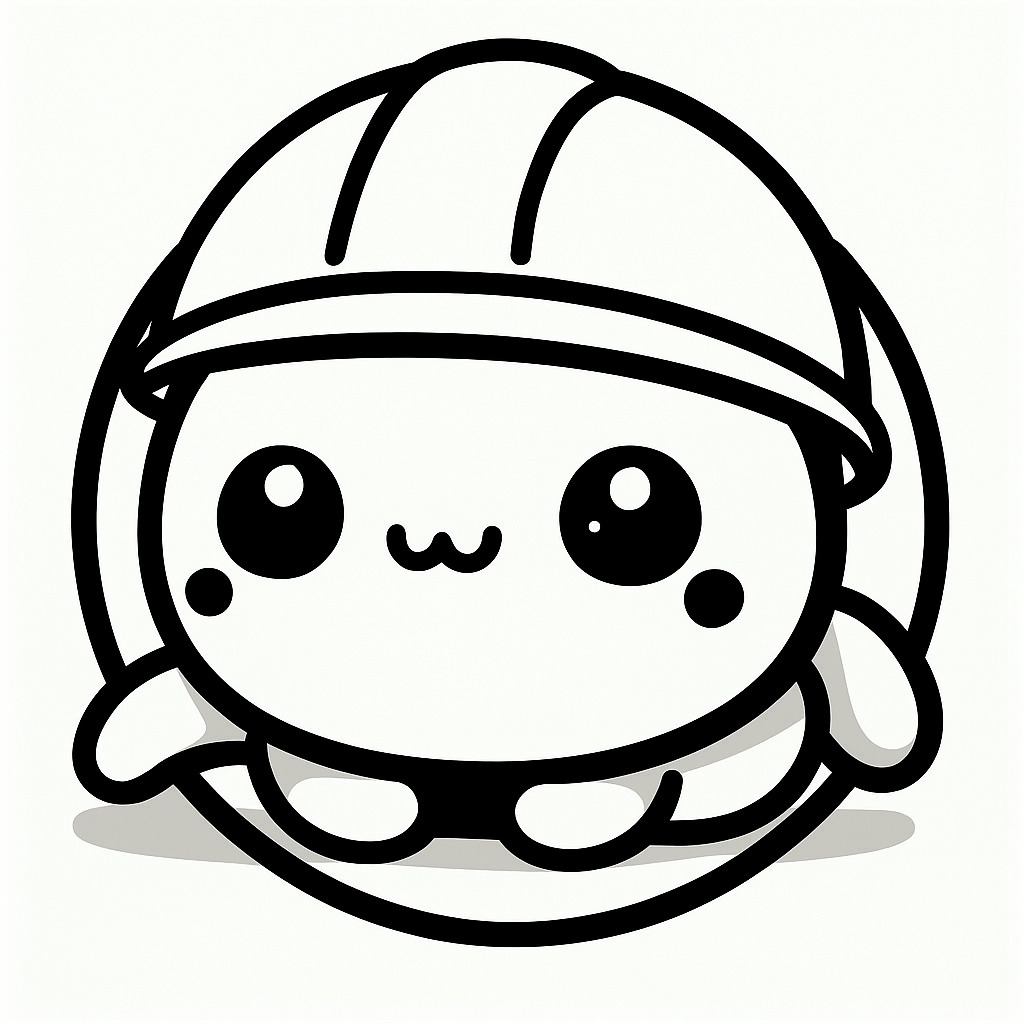
「積み残し」って、気づいた時にはもう出発してるってこともあるから、事前の仕掛けが命なんです😊
コメント